Open-cell foam against rafters?

I live in Connecticut and recently had a home energy audit, and the main issue they found is that my attic is not insulated enough. My attic floor is insulated [not enough] and covered in plywood as we use it for storage. It also contains an air blower for forced hot air [hot water comes from boiler in basement] and AC.
I have contacted three different spray foam contractors and they all recommend spray foaming my rafters and foaming over my soffit and ridge vents creating a conditioned space. Two of the vendors will do close cell foam although I had to specifically request closed cell as their first reco was open cell. The third only does open cell and is strongly recommending open cell. He says you want open cell so the system can breathe and “not” trap moisture.
None of these three contractors recommended a vapor barrier if were to use open cell.
I checking my building codes:http://www.ct.gov/dps/lib/dps/office_of_state_building_inspector_files/2009_amendment_final_unformatted.pdf发现了这个:“一个air-impermeable insulation is applied in direct contact to the underside/interior of the structural roof deck. “Air-impermeable” shall be defined by ASTM E 283-04. “
I also found this article here://m.etiketa4.com/green-basics/spray-foam-insulation-open-and-closed-cell: “Open-cell foam is relatively vapor-permeable. Three inches of open-cell foam have a permeance of 16 perms. When installed in a cold climate, the interior face of open-cell SPF should be covered with a vapor retarder (for example, vapor-retarding paint”
I’m distressed that I can’t find a contractor that will offer me a solution that meets everything I read online. I’m starting to second guess myself, but this is what I think NEEDS to be done as not to prevent a moisture problem:
– CLOSED cell foam against the roof rafters
– Ensure all gable walls are spray foamed
– Spray soffit and ridge vents to create a conditioned space
OR
– OPEN cell foam against the roof rafters
– Ensure all gable walls are spray foamed
– Spray soffit and ridge vents to create a conditioned space
– AND apply some sort of vapor barrier in the interior
Is all my research correct? Can anyone recommend a spray foam contractor in CT that will do this work?
GBA Detail Library
A collection of one thousand construction details organized by climate and house part
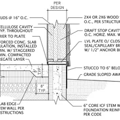
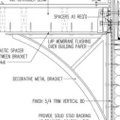
Replies
Frank,
Your research is correct.
1. Both open-cell and closed-cell spray foam are NOT air-permeable.
2. Open-cell spray foam is vapor-permeable; closed-cell is not.
3. Either product can work in this application, but in your climate, it's important to include an interior vapor retarder (usually a coat of vapor-retarder paint, sprayed on the inside surface of the cured foam) if you choose to install open-cell foam. Without the vapor retarder, the roof sheathing can accumulate moisture during the winter.
4. Most codes require the foam to be protected on the interior with an ignition barrier. Gypsum drywall is best, although many spray foam contractors suggest an intumescent coating. These intumescent coatings are somewhat controversial.
5. Many spray-foam contractors try to talk homeowners into accepting foam installations with less than the minimum R-value required by code. Don't agree to such an installation. You are in Zone 5, so you need a minimum of R-38 insulation -- at least 6 inches of closed-cell foam or 10 inches of open-cell foam.
6. For more information, see:
Creating a Conditioned Atticand
It’s OK to Skimp On Insulation, Icynene Says.
Martin
You recommended a vapor retarder on the underside of the foam, I've not seen that in my climate (hot-humid, Gulf Coast). Do you recommend it in this climate? By the way, I typically have Ice & Water Shield on the roof if that makes a difference. I am not aware of moisture issues, but then maybe I've just missed them. What is your advice.
You mentioned a thermal barrier, did you mean ignition barrier? I think that is required in attics now as of 1-1-11.
Allan
Allan,
1. The vapor retarder is only required in cold climates -- Connecticut / Massachusetts or colder. In Texas, it's unnecessary.
2. You're right, of course -- I meant ignition barrier, not thermal barrier. An ignition barrier is a less stringent requirement than a thermal barrier. Thanks for catching my error. I have corrected the word in my original answer.
Thanks Martin. I wish you would delve a bit deeper into the R-value used in attics by spray foam contractors in this climate. We typically do R-38 for attic insulation but when doing non vented attics I believe a lessor R-value is recommended, maybe R-19? Please don't dismiss this out of hand, there may be a valid reason, it does seem to be working in moderating attic temperatures.
I am looking for ways in my homes to keep equipment and ducts out of attics, and using spray foam only in the walls. It is very difficult in larger homes with 5-6 separate systems, but I currently have a spec house I started and I think I can accomplish this.
Allan,
Of course R-19 is effective at lowering attic temperatures. It just isn't as effective as R-38. In fact, the rate of heat flow through an R-19 roof assembly is exactly twice that of the rate of heat flow through an R-38 assembly.
Double the insulation R-value, and you cut the heat flow in half.
Thanks for the info and confirmation Martin. Regarding an ignition barrier, I found this in our building codes of ct:http://www.ct.gov/dps/lib/dps/office_of_state_building_inspector_files/2009_amendment_final_unformatted.pdf
(Amd) R314.2.3 Attics and crawlspaces. Within attics and crawlspaces
where entry is made only for service of utilities, foam plastics shall be
protected against ignition by 1 ½-inch-thick mineral fiber insulation, ¼-
inch-thick wood structural panels, 3/8-inch particleboard, ¼-inch
hardboard, 3/8-inch gypsum board or corrosion-resistant steel having a
base metal thickness of 0.016 inch. The ignition barrier is not required
where the foam plastic insulation has been tested in accordance with
Section R314.3.
(Amd) R314.3 Specific approval. Foam plastic not meeting the
R314.1和R314.2可能要求的部分specifically
approved on the basis of one of the following approved tests: FM 4880,
UL 1040, NFPA 286 with the acceptance criteria of Section R315.4, or
UL 1715, or fire tests related to actual end-use configurations. The
specific approval shall be based on the actual end-use configuration and
shall be performed on the finished foam plastic assembly in the
maximum thickness intended for use. Assemblies tested shall include
seams, joints and other typical details used in the installation of the
assembly and shall be tested in the manner intended for use.
How do I know if the spray foam I'm going to use meets these tests R314.3 and do not need an ignition barrier like dry wall?
"How do I know if the spray foam I'm going to use meets these tests R314.3 and do not need an ignition barrier like dry wall?"
Ask the supplier/installer for documentation.
Frank,
All the foam manufacturers are testing their materials to determine compatibility with the new standards. This is an ongoing process. To my knowledge, there are no open-cell materials certified for unprotected use in attic spaces (ref the language of your building code) but there are several closed cell products that can be used. Contact your contractors and ask to see the ICC reports on their foam.
Adding a proper ignition barrier coating to open cell foam is difficult and expensive and we now recommend certified closed cell foam to our customers. You need 6 inches to achieve r-38.