Opinions on This Building Plan

Hi,
Planning for a future new home build in Climate zone 6a.
I’m looking to detail an exterior wall insulation system that is high performance, affordable, and easy to install. Since I am still able bodied, I’m willing to take on some of the air sealing and energy efficiency items myself, while having a custom builder handle a majority of the work.
I don’t like the idea of attaching strapping and siding through thick exterior foam or rigid mineral wool, so I was thinking of doing a hybrid system of the following.
1. Frame and sheathe house normally with 2×6 framing. . Exterior plywood seams to be taped with Zip tape. This would be the primary air barrier.
2. Cut 2” foam strips and fasten to 2”x”3 nailers. These would be fastened to the sheathed wall at the same location as the structural studs. Depth of this cavity would be 3.5”. The foam would be to the inside, tight against the sheathing. Nailers to be fastened with 5.5” to 6” long nails through one of the new school Big Bertha framing guns. (The cost savings of using nails instead of long screws exceeds the cost of the nail gun)
3. Install R-15 3.5” thick mineral wool batts between the nailers. Mineral wool batts would probably need to be ripped about 1” narrow because of the extra width of the 2x3s. Conventional WRB like Tyvek would be installed on the outside of the assembly and detailed conventionally.
4.安装绝缘垫的另一种类型inside. Possibly r-21 fiberglass batts, with Membrain vapor retarder, and GWB sheathing.
Even at inflated material prices, I can install the insulated nailers and mineral wool exterior foam insulation for under $1/sf if I do the labor for this portion.
Advantages: Framing lumber would be thermally broken to R-8 or better, wall cavities would be insulated to R-36, any bulk water that bypassed the WRB should in theory drain through the mineral wool, mineral wool batts are much cheaper than rigid foam or rigid mineral board sheets, no area is lost to the inside footprint of the house.
Disadvantages: Framing is not insulated as well as the cavity areas, there would be no air gap behind the siding as in a conventional rain screen (bumpy wrap could be used), tricky detailing to keep rodents and bugs out of the exterior mineral wool.
—General thoughts on this assembly?
—Any ideas on how the bottom portion of the mineral wool could be protected while still allowed to drain?
—Any other disadvantages can you predict?
—Does this seem “conventional enough” to not get charged an arm and a leg by framing or siding contractors who may not be familiar with green building techniques?
TYIA
—Rick
GBA Detail Library
A collection of one thousand construction details organized by climate and house part
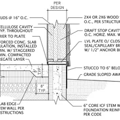
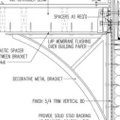
Replies
I am a fascinated amateur not a pro. Your proposed wall description written out like that without details is hard for me to visualize. I wouldn't want to mislead you.
I like the way Joe Lstiburek describes what is going in walls. If you are interested:
https://www.buildingscience.com/conversations-and-videos
I your climate zone it gets cold and it is a moist zone. So, there will be condensation in the wall in the winter. Where will the condensation point in the wall be on cold winter nights and how will the moisture dry and get out of there?
If you haven't seen Cup of Joe with Joe they are worth a look.
What your are proposing should work but a lot of labor. I think ripping up some R9/R12 ZIP into strips and nailing it up would be much less work and time.
You can skip the foam plus nailer and nail up 2x4 on edge at 90 degrees to your studs. This gets you most of the thermal bridging reduction but much quicker to install. You can cut a groove on the back of the 2x4 for drainage or space it off with a bit of 1/4" ply. This would also let you use standard batts and you can install something like board and batten or metal panels directly onto these horizontal 2x4s. I've done this type of assembly on for roofs. Pretty simple to build.
Probably the bigger issue with this type of detail is your openings. Simplest is probably to go with outies and put the windows onto bucks. It will mean some flashing tape origami back to your WRB layer but it would make your siding install pretty "standard".
Seems to me you are buying all the framing wood to build a double wall and spending extra labor to put the plywood in center and then choosing more expensive insulation to fill the walls.
I say build the double wall and fill it with cellulose.
Generally fiberglass batts end up installed poorly and under perform.
The most important thing a wall does is hold up the roof next it must keep out the rain and you glossed over that part of how you will build the wall.
Walta
我认为,一个mount of work you're adding to try to avoid the work of attaching things through exterior rigid foam will exceed the amount of work it would take to just attach things through the exterior rigid foam. Basically I think your "solution" is going to make things even harder for you compared to the original "problem".
I think you'd be better off doing things the usual way, with continous exterior rigid foam and 1x4 or plywood strips (I prefer strips of 3/4" plywood) fastened through the foam to provide an attachment point for siding.
I would use mineral wool on the interior side instead of fiberglass, althought either would work. For bottom edge protection, stainless steel mesh screening will work, and there are also purpose-made perforated aluminum channels that will work. I usually use stainless mesh myself. If you really want to stick with your plan, then I'd take Akos' suggestion to save at least a little labor.
You want to plan for things to go as much like an assembly line as possible, so the more modifying of existing products you have to do, the longer things will take. I can tell you from personal expierience that cutting rigid foam into pieces that will fit between studs is much easier than cutting mineral wool batts too. Mineral wool is softer, but it's harder to get a straight cut over a long distance, and you'd be surprised how much time you'll burn cutting lots of batts down to size.
If you put full-size sheets of rigid foam up, all you have to do is hit the studs through that foam when hanging furring strips. The full-size sheets of foam avoid all the cutting, except maybe a sheet at the end of the wall, and all the extra structural details are avoided as well. All you're left with is hitting the studs through the foam, which really isn't that bad if you use a jig (I have described a simple jig for this on GBA in the past, made from a scrap of 2x4).
Bill
Just thinking about the current cost of lumber.
The 2x4s needed to cross strap would cost the same as a sheet of 4x8 roofing polyiso. If you add in the cost of insulation, your assembly is above the cost of going for rigid insulation and more labour.