Rafter health for unvented cathedral ceiling insulated with SPF

One of the methods of insulating an unvented cathedral ceiling is enough closed-cell SPF insulation below and directly in contact with the roof sheathing, with fluffy insulation below. Compared to EPS installed above the roof sheathing, this saves one layer of sheathing, eliminates long screws, and increases fire resistance (SPF vs. EPS). The downsides include rafter thermal bridging and high SPF cost.
The question I have has to do with how the rafters in this roof structure behave with water vapor and condensation. My understanding is that you need to have enough SPF directly below the sheathing so that the condensation plane is within the SPF. However, it appears that the condensation plane would also occur within the rafters, but perhaps at a different depth. Why is this not an issue? Is there a potential difference in long-term rafter health for this design among dimensional lumber, I-beams, and engineered lumber beams?
If it makes any difference for this question, house location is northeastern Oregon, Climate Zone 5, with 24 inches of precipitation per year.
Thanks,
Steve
GBA Detail Library
A collection of one thousand construction details organized by climate and house part
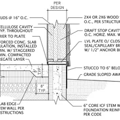
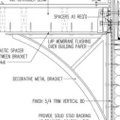
Replies
Steve,
The short answer to your question is that condensation doesn't occur inside wood -- or even on the exterior face of a piece of lumber. Since wood is porous, what occurs (when increasing quantities of water vapor come in contact with wood) is sorption. Through sorption, the moisture content of a rafter may rise. But there won't be any condensation.
If a piece of wood is very cold, and very warm moist air comes in contact with the very cold wood, frost can build up on the cold wood. But your rafters will never get cold enough for frost to form under the circumstances you have described.
Finally, most condensation scenarios in cathedral ceilings involve air leaks that allow humid indoor air to pass near to a very cold surface. If you have a good air barrier at the ceiling level, you won't have that kind of air movement, and you've nipped 95% of potential moisture problems in the bud.
Thermal bridging through rafters is a problem, but (a) it is a relatively minor problem, and (b) it's a heat flow problem, not a moisture problem.
The vapor permeability of most framing lumber is comparable to that of 2lb polyurethane (same order of magnitude, anyway). Log homes don't rot from wintertime moisture adsorption even without installing interior side vapor barriers, and neither will rafters that extend through a layer of closed cell foam.
SPF that is exposed to the exterior isn't signficantly more fire-safe than EPS above the roof deck. The roof deck is a thermal barrier against ignition. Polyiso is in the same chemical class as polyurethane, and comparable in cost per R as EPS. Even when derated for temperature inch for inch it'll outperform uprated EPS in your climate.
There isn't really such a thing as a "condensation plane" at some depth within the building assembly. I'm taking your terminology to mean the point withing the material where the wintertime average temperature is approximately the same as the average wintertime dew point of the interior air. Both the dewpoints and temperatures will change daily/hourly- only the longer term averages matter from a moisture accumulation perspective.
Problems occur when wetting rate exceeds drying and moisture accumulates. This can occur when you have both a source of water vapor (eg, airflow from the interior) and a condensing temperature. The middle of a wood beam has too little of the former.
Martin, Thank you for your clarification.
Dana and Jon, Thank you for the clarification of dimensional lumber permeability. What about I-beams or engineered lumber beams? I will need ~16in depth to get the R-value I am looking for, so engineered solutions would be simpler than adding gussets and 2X2s to 2X10 or 2X12 rafters. In addition, due to windows, doors, and open space directly below the ridge throughout the house, a structural ridge beam and post support of the roof wood be difficult. Therefore, a collar-tie is probably necessary. Due to collar tie length of 24-28ft, engineered lumber beams would probably be required (for the collar ties) and the ends would extend into the insulated roof cavity. Is this a problem?
Dana, perhaps I am misinformed, but my understanding is that SPF is self-extinguishing and does not melt and lose its structure when exposed to fire (similar to polyiso), whereas EPS will continue to burn and melt when ignited. In the data I have looked at, I would agree that polyiso would perform fine at typical winter temperatures, but it's not so clear that at extremes (-20 to -30F), it would perform well. Although the cold temperature performance of polyiso doesn't seem likely to create a structural issue, it could result in a comfort issue (although for only a few days in a typical decade).
When dry OSB in I-beams has somewhat lower vapor permeabilty than SPF, a bit more vapor tight than milled lumber. At a wood moisture content high enough to be a mold problem OSB is about 5x as permeable as SPF. It's still the same order of magnitude.
SPF is not self extinguishing, neither is polyiso, but it's correct that neither will melt. But EPS on the exterior of a roof deck with a nailer deck above it isn't a fire hazard. By the time the fire burns through a deck and the EPS lights off the house is pretty much gone.
In zone 5 it doesn't really get to -20F or lower long or often enough to matter, but even the WORST grades of polyiso would be delivering better than R2/inch when it's -30F outside, 70F inside and the polyiso is 40% of the labeled R. (In my own zone 5A location it's hit the negative teens fewer than 5 times in the past 25 years, and the all time record low temp here is -18F which happened more than 80 years ago.) If you have (labeled) R20 polyiso on the exterior of a fiber R30, and the R20 is really only performing at R6 during the coldest hours since the last ice age you still have R36, which is definitely NOT going to be a comfort problem as long as your heating system has the capacity to cover that fairly small difference in BTU/hr:
在热损失R50温度均在100 fnce is about 2 BTU per square foot, at R40 it's about 2.8 BTU per square foot. For 2000 square feet of roof the 0.8 BTU/hr per square foot difference adds up to 0nly 1600 BTU/hr- less than 500 watts. You may have comfort issues when it's -30F outside, but it's more likely to be related to window performance than roof performance.
Steve- have you thought about using scissor trusses? You can get the cathedral ceiling, insulate with cellulose, vent the roof , skip the collar ties and expensive spray foam.
Dana, the closest official weather station to the build site (<5 miles) shows a historical low of -31F and an average annual lowest temperature of -13F. I have been at the build site when the temperature was -20F. However, average winter temperature is closer to 25-30F. In addition, in thinking more about my comments on comfort, your points are well taken. The primary heating in spring and fall and part of winter will probably be a minisplit that does not have the capacity or the cold weather performance to heat the house at -20F. Code compliance backup would be electric resistance (very low install cost). Primary heat during winter will be a wood stove, and the issue there is excessive heat production and not whether there is enough heat available at -20 or -30F, regardless of (reasonable) insulation R-values.
Stephen, thanks for the mention of scissor trusses. I had not considered them because the typical use seems to be (as you describe), a ventilated roof assembly. Because the house is being built in a high wildfire risk area, I prefer an unventilated roof to prevent the potential for embers to enter the roof assembly. However, I realized that it would be possible to build an unvented cathedral ceiling using raised-heel scissor trusses. Of course, Martin has already addressed this possibility in one of his articles. One way of building a cathedral ceiling this way is through using closed cell SPF against the sheathing and then open-cell SPF to reach the desired R-value. This also has the advantage of reducing thermal bridging. It is possible that I might end up with a conventional ventilated roof due to cost. If so, there are Class A fire rated ridge vents and fire blocking soffit vents (e.g. Vulcan) that are approved in California wildfire prone areas (not required in Oregon yet, but could be in the next few years).