Understanding vapor transmission and perms

I understand the different levels of vapor retarders and how a lower perm rating means less vapor comes through the material. What I don’t understand is how this affects the amount of water vapor coming through in real life.
例如,假设我有一个完全未完成的地下室,带有潮湿的壁,在地下室导致湿度很高。如果我用0.5 pers蒸气阻滞剂覆盖墙壁,这将如何影响室内湿度?如果我使用蒸气屏障,那会带来多少差异?PERMS与产生的室内湿度之间的关系是线性的吗?
GBA Detail Library
由气候和房屋部分组织的一千个建筑细节的集合
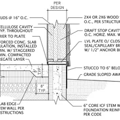
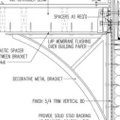
Replies
缺口,
No, it's not a linear relationship, for a variety of reasons:
1. There is more than one source of water vapor entering a house.
2. Occupants and plumbing usually introduce water vapor.
3. Indoor relative humidity is affected by the outdoor temperature and the outdoor relative humidity.
4.室内相对湿度受炉,通风风扇,除湿机和空调等HVAC设备的操作影响。
In other words, there are many, many factors affecting indoor RH. If your wall assembly is vapor-permeable, and the wall assembly starts out dry, it's even possible for a thick, dry wall that is filled with hygroscopic insulation materials to lower the indoor RH (for example, when occupants take showers) by absorbing moisture.
缺口,
One more thing: I don't recommend that you try to install a layer of polyethylene on the interior side of your basement wall. It would be much better to install a layer of rigid foam instead. For more information, see如何隔离地下室墙.
我不会安装poly,但是有许多刚性泡沫具有蒸气屏障的面孔。因此,例如,未取消EPS和箔纸泡沫之间的现实世界差异会有什么?假设地下室没有任何其他重要的湿度来源,并且地面总是潮湿的。这确实与我的现实世界地下室有关,但我也想从学术意义上理解这一点。
缺口,
Thin EPS is vapor-permeable, so when installed on a basement wall, the thin EPS would allow moisture to diffuse from the damp basement wall to the interior.
On the other hand, foil-faced EPS or foil-faced polyiso is a vapor barrier, so when these products are installed on a basement wall, they prevent vapor diffusion from the wall to the interior.
Martin, I understand the zero-versus-some difference between the two. I'm looking to quantify the "some" in a way that I can understand. I don't know how to translate "grains per inch of mercury" to something tangible.
缺口,
To get a handle on permeance, Joe Lstiburek's three classes of materials is as good a method as any:
Class I vapor retarders: 0.1 perm or less (sheet polyethylene, non-perforated aluminum foil)
Class II vapor retarders: more than 0.1 perm but less than or equal to 1.0 perm (kraft-faced fiberglass batts)
Class III vapor retarders: more than 1.0 perm but less than or equal to 10 perms (latex or enamel paint)
Class I vapor retarders are what we used to call vapor barriers.
Class II vapor retarders allow a little bit of diffusion.
Class III vapor retarders allow some drying (or diffusion) -- significantly more than Class II retarders -- but they aren't wide open.
If you have a wall with especially high dampness it's best to deal with the drainage issues first. If you stem drying toward the interior and the concrete saturates, it will have to dry toward exterior at the above-ground section of the foundation, or potentially into the foundation sill if there isn't enough exposure for drying above grade. (About 18" would be plenty no matter how wet the foundation is, but less than 12" could have some risk.) Is there any efflorescent growing on the interior side of that wall?
为了使水蒸气在组件上移动,必须有蒸气压差。升高温度会增加蒸气压力,从而降低温度。
On the dirt side of the foundation it's a nearly saturated 100% RH, but it's at whatever temperature that is. The basement will be running a higher temperature, but a lower RH. At some RH less than 100% the vapor pressures will equalize, and no more moisture diffuses from the dirt into the basement, but that may be at a higher-than healthy RH. When a cool damp foundation wall is exposed to a drier room air, it will keep evaporating into the room air until the vapor pressures are equal. What you are trying to do is slow that down to something tolerable, something that is easily handled by the HVAC or dehumidifier systems.
当您在凉爽的气候下安装隔热材料(任何类型)时,在凉爽的气候下,在混凝土滴的内表面的温度(和蒸气压),因为混凝土表面的温度大致变为土壤的温度而不是地下室的房间。仅此一项就可以减少蒸气压差一些,但也许还不够(?)。这取决于您的房间rh限制限制是什么。
0.5 pers蒸气阻滞剂实际上是一种相当强大的蒸气阻滞剂,而通风率和HVAC系统对房间的湿度水平的影响要大得多,而不是将其降低到带有一张poly的0.05 perms。如果您要整理房间,甚至5个perms vs. 0.05 Perms在房间Rh。都不会带来很大的不同,但是如果您要建造成品螺柱,则可能会成为一个问题。理想情况下,您希望在鞋座范式中您需要蒸气渗透到基础墙和螺柱上的易感木材和石膏面之间的蒸气,以等于或低于饰面涂料,以便在易感层中的湿度,房间的湿度,而不是土壤的湿度。
This isn't super-simple stuff to model in multi-material assemblies, which is why the Fraunhofer Institute came up the WUFI model for simulating heat & moisture transfer across assemblies. But as some folks at the Building Science Corp like to point out, if you have to run a WUFI simulation to know if the assembly makes it or not it's probably not a very resilient assembly. A really crude first order rule of thumb is usually good enough:
如果组件的冷侧的蒸气渗透率小于条件侧,则不会有太多从该侧移动到条件空间的水分。但是,如果凉爽得多,则可以从温暖的一面向凉爽的一侧进行大量的水分迁移,这取决于该侧相对于条件空气空气的露点以及内部侧面的蒸气渗透。在地下室情况下,从房间转移到粉底的冷混凝土中,水分绝不是问题,但是如果墙壁堆栈中的易感材料下降到房间温度的露点以下,这可能会成为一个问题。因此,通常是一个好主意腔。
使用IRC规定值在使用III类内部侧蒸气延迟器时,使用木质结构护套在木制结构护套上进行绝缘,适合基础墙 - 甚至更具余量。((http://publicecodes.cyberregs.com/icod/irc/2012/icod_irc_2012_7_sec002_par025.htm_ But in the basement case it's best to use air-impermeable insulation between the concrete particularly on the above-grade section of the foundation. Since even an inch of Type-II EPS has a vapor retardency comparable to or less than latex paint- it's enough to effectively limit the sub-grade migration of ground moisture through the studwall to rates the studwall can tolerate. At 3" (R12.6) it's a class-II vapor retarder.
回答这个问题:
如果您在两侧的蒸气屏障均具有相同的温度,但固定的湿度不同,那么经过的水分量与PERM成正比。0.5 pers将有一半的水分通过1 pers(尽管两者都很小)。
As the discussion above shows, there are lots of reasons that your example is unlikely to match the simple scenario I described. Adding a vapor barrier might result in the wall being more damp, so the humidity isn't independent of the vapor retarder/barrier you choose. And the temperature of the wall is quite likely cooler than the room....in some cases, the cool wall is damp because the room is humid, rather than the room being humid because the wall is damp.
Now replying to Dana,
感谢您对许多复杂问题的良好解释。
关于咒语,“如果你要运行一个WUFI年代imulation to know if the assembly makes it or not it's probably not a very resilient assembly," I agree, but on the other hand, WUFI can be a great tool for learning what assemblies are more or less resilient, and when they are likely to get into trouble. The free educational version of WUFI has some limits that make it hard to use for verifying performance of a particular assembly in a particular climate, but for teaching yourself how various factors influence performance, it can be very helpful.
Regarding "Using the IRC prescriptive values for insulating sheathing over wooden structural sheathing when using class-III interior side vapor retarders works just fine for foundation walls- it even has more margin," that makes sense if your worry is winter condensation. However, in a basement, the worst time can be spring or summer--spring because the foundation wall is still very cold while the indoor humidity is getting higher than it was in winter, or summer because that can be when there is the biggest temperature difference between the hot, humid indoor air and the cool foundation particularly near the floor.
真的是一个通过foam-R /厚度问题ertime thing. Yes, the foundation is colder than the dew point of the room air in spring, but it's still quite a bit warmer than the above grade section of the wall in the dead of winter.
Assuming you limit the basement's RH to 60% there is no scenario where the foam/fiber interface lingers at or below the dew point of the interior air long enough to matter in spring if you go with the IRC prescriptive levels for wood sheathed above grade walls. At 70F/60% RH the dew point is about 55-56F. As a dumb first-order approximation, ahead and calculate how cold the foundation has to be for the temp at the foam/fiber interface to be in the 55F condensing zone, and how long that would be likely to persist with the warming trends of spring/summer. It doesn't take WUFI to figure this one out either- there's plenty of built-in margin in the IRC prescriptives when applied to foundation walls.
eg: In zone 5 the prescriptive is R5 for 2x4 walls. Assuming a 2x4 wall with R15 fiber and R5 foam, in a 70F room that's a 15F delta-T over the R15, or R1 per degree F. That means the foundation would have to persist at 5F colder than 55F or 50F over a couple of months. Since the even the deep subsoil temps in any zone 5 location would not be substantially below 50F, while there may be an early spring period where the foundation was below 50F when the interior air dew point hit 55F that would not persist into summer. In early spring it's unlikely that basement air would reach a dew point that high even at modest ventilation rates.
比较深层土壤图与气候区图,并使用IRC规定数字运行哑光线性露点模型。为了使夏季露点成为一个问题,地下土壤必须变得更酷,以便使用这些R-Ratios在Studwall腔内产生露点问题。
http://www.builditsolar.com/Projects/Cooling/US-ground-temps.gif
http://www.energyvanguard.com/Portals/88935/images/iecc-climate-zone-map-energy-code-warm-moist-line-800.jpg
Thanks Dana, for addressing the question of when condensation is worst in so much detail. I think the reason we came to different conclusions is that you assumed the basement temperature and humidity are limited, whereas I was thinking of a scenario in which the windows are open and the outside is, for example, 80 F and 75% humidity. The basement probably won't get up to 80F, but with enough air flow it could have the same absolute humidity as the outside air, which means a dew point of 71 F. If the concrete is 60 F and the room is 75 F, for your example of R5 foam and R15 stud walls, there's condensation throughout more than half of the stud wall.
So if you build that way, you are building in a requirement for dehumidifying that space. You might argue that it should be dehumidified no matter what, but the amount of dehumidification necessary to avoid condensation in moisture sensitive materials is more with the R5 foam and R15 fiberglass than it would be with R20 foam, and it seems to be to be better to build a building that is tolerant of various occupant behavior patterns.
You don't want to over-ventilate any part of your house with latent loads that high.
The outdoor dew points at my house in central MA are often several degrees warmer than my basement (even when there is no sensible air conditioning load to speak of) so even though my foundation insulation is an all-foam solution there would be severe mold issues.
The solution is to not ventilate more than the minimum required for reasonable air quality, and purge the moisture mechanically. As it happens my shading factors leave me with very low sensible loads, but the latent loads are very real.
Basically, any insulated house in a humid climate will need dehumidification, including the basement. An RH of 60% is something of an upper bound for comfort & human health (50% is an upper bound for those allergic to dust mites.) And that goes for the basement as well.
Dana, we agree about the need for dehumidification, and we agree about the physics of when problems might happen. Our difference is only that I am more conservative about wanting to design a basement to be more tolerant of a wider variety of occupant behavior. Some people like having the windows open in the summer even if it is hotter and more humid than would be ideal for comfort and dusty mite control. I'm not arguing that that is a good idea--I'm only arguing that it happens.