Polyiso vs. EPS Foam Insulation Over Stucco
我在新墨西哥州高沙漠(5B区)有灰泥房屋。灰泥在被以前的所有者严重虐待之后,状况不佳,因此我借此机会将整个房子包裹在连续的刚性绝缘材料中,作为Re-Stucco项目的一部分。这些木板将用于现有的恶化灰泥,固定在其及其护套上和螺柱上,然后将附着一个新的1/2英寸两层胶结灰泥覆层。
They say they can only use a maximum of 1.5″ of foam because they’ll need to use masonry nails to attach it to the studs because the nails have to penetrate the stucco, and the thickness of the stucco and the Celotex sheathing plus 1.5 inches of foam (2.75″ total) is the most they can do to allow the nails to penetrate the required once inch into the studs given that the longest masonry nails they have are 4″.
I have two options for the foam: Polyiso or EPS. The bid is about $11k ($9.50/square foot) for Polyiso and $10k ($8.60/square foot) for EPS. Here are my estimates of the foams’ long-term R-values in my climate (taking into account Polyiso’s R-value reduction over time and the performance characteristics of Polyiso and EPS in different temperatures as documented in the “Polyiso Penalty” article:
Polyiso R-7.5 in the heat; R-6.7 in the cold
EPS R-5.7 in the heat; R-6.8 in the cold
Either choice would exceed the code-minimum of R-5 for continuous insulation applied over 2×4 studs in climate zone 5.
I’m considering going with the EPS option for the following reasons:
1.低upfront price.
2. My manual J modeling shows that it’s basically a wash: compared to EPS, Polyiso yields a lower summer peak cooling load by 200 BTUs, but the peak heating load is increased by 80. Big whoop.
3. My peak heating is much more expensive than my peak cooling (horrible oversized 80% efficient gas furnace @ $1.25/hour for 2 hours a day vs a wonderful swamp cooler @ $0.06/hour for 12 hours a day); the better cooling performance is likely to produce few financial gains.
人们怎么看?我有什么忽略的吗?我应该选择Polyiso而不是EPS的任何原因吗?只有1.5英寸的EP可能会带来很大的不同吗?
GBA Detail Library
A collection of one thousand construction details organized by climate and house part
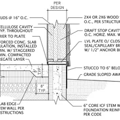
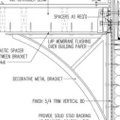
Replies
Another reason you might want to go with EPS is the wall is built up with poly or foil under the interior gypsum, or if you have foil or vinyl wallpaper on the interior. Foil faced polyiso is an extreme vapor barrier, less than 0.05 perms, whereas unfaced 1.5" of EPS is still in the ~1.5-2 perm range, offering a real drying path toward the exterior.
Even if you went with fiber-faced polyiso, most versions are still guaranteed to be less than 1 perm (but might test higher than 0.5 perms, depending on facers and thickness.)
There's no interior poly or foil or any wallpaper. I've opened the wall in multiple places from both the inside and out in the process of doing DIY projects so I know what's in it. Here's the current wall sandwich:
- Many layers of latex paint (40 year old house)
- Drywall
- 2x4 studs with 2" R-8 kraft-faced mineral wool in the cavities, terribly installed
- Celotex sheathing
- Single layer of tar paper
- Chicken wire stucco lath
- 3/4" cementitious three-coat stucco
- Latex paint (ugh, this makes me so sad)
- Cementitious stucco color and texture coat (peeling off in a million places, naturally, as it didn't stick to the paint)
Here's what will be added:
- 1.5" EPS or Polyiso
- More chicken wire stucco lath
- 1/2" cementitious two-coat stucco
FWIW, this area gets less than 9 inches of rain per year. Water management detailing around here is poor, I suspect because builders realized they could safely get away with it. There is no sign of moisture damage anywhere and relative humidity hovers below 30% year-round unless I'm running the swamp cooler.
It's worth packing in cellulose from the exterior before adding foam, which will reduce any convection through the cavity from the interior side. If you do that you'd be winter-safe even with foil faced polyiso (if that's what you choose.)
If you don't completely fill the cavities it's likely the R8 econobatts won't block much convection from the interior. Even if installed perfectly the studwall + original stucco with econobatts is giving you at best R5-ish performance, and filling the cavities with fiber (any type or density) will bump to about R9-10. If the batts are still hanging OK rather than balled/bunched up in sections it should be possible to dense-pack it, but even if you have to poke 3 -5 holes in to fill the cavities in a more haphazard way to get round deteriorated batts it would be good enough even with 2-2.5lb cellulose. With fiberglass it needs to be 1.8lb density to get the air-retardency, which is a dense-packed density for fiberglass (but not for cellulose.)
Nathaniel, I think your decision logic makes sense. It seems a little crazy that there are no longer masonry nails available, but you'll have pretty good results with 1.5", so it might not be worth inventing a different solution.
Nathaniel,
我想知道如果你完成你的分sion for your home. I'm in ABQ and am debating an identical/very similar project. Wouldn't mind knowing how the project has progressed. We're debating extending the parapets, turning the stucco system over the top, terminating into a PTO roof over Polyiso/EPS (a chance to avoid the New Mexico roof diaper look when using a membrane roof, and removal of roof cavity venting; turning the system into a "hot roof").
Funny you should mention it. The foam is being applied at this very moment! So far I'm pretty happy. I'm only gaining about R-6, but it's probably doubling the effective R-value for the wall on this old tract house. The only thing I would have preferred is thicker foam, but it was limited by the length of the masonry nails they could source. After having busted up a bunch of the stucco to redo the windows, I honestly think removing the stucco entirely would have been an option. I could have just pulled it off in sheets! And that would have allowed any foam thickness I wanted because they could have used like 8" screws or something. Oh well,
Would you be willing to share some of the construction details? (eg Termination at base of wall, parapet, etc). I've attached a PDF of my basic ideas for the system... will be drawing it up over the next few months.
So far it looks to me like they're doing things right. They terminated the base with a weep screed on the bottom of the new wall assembly (previously there was none), they're taping the seams, and they're lathing over it in a manner that looks to my untrained eye to be indicative of quality work. My house has a pitched roof so there are no parapets.
And for what it's worth, it's made a huge difference already. The house feels noticeably warmer with fewer cold spots, and the furnace doesn't come on as often.
Hey Nate! I am in ABQ and looking to do a very similar project. Are you willing to share who you used and whether you are happy with the work? The only diff is my house is an older Adobe.
Hi Nate,
I am in Southern NM. 1000s of older houses down here could benefit from what you are doing. I hope you will add to this post from time to time. Whatever you can give from your experience might benefit many. Is adding rigid foam to the outside of traditional stucco getting to be common in ABQ or are you breaking ground? Thanks!