Adding attic insulation to my 1983 suburban Atlanta home

Hi there,
I love this website and community and have found it indispensable these last few months since I purchased my most recent house that was built in 1983. I’m in the process of making some investments into energy-efficient upgrades including new HVAC systems and additional air sealing and insulation in the attic. My initial design approach was to create a small mechanical closet on the upstairs level to house the new air handler for the heat pump. Unfortunately, there’s no option to pull the ductwork out of the attic so that has to stay as-is. Yes it’s fairly leaky but good news its hard metal duct in pretty good condition otherwise. I thought this approach was likely my best option for installation all things considered.
However, one of the HVAC contractors quoting the project suggested I get the attic insulated with spray foam under the roof sheathing. I’m in the Atlanta area so zone 3 mixed humid climate. I know this can be done as long as done carefully with an eye toward creating an adequate moisture barrier using closed-cell foam or by creating an air channel for the soffit/ridge vent system to continue to function. The attic is currently insulated with fiberglass batts between the joists at the second-floor ceiling that are overfilling the joists with an R-30 batt. Nothing in the drywall ceiling plane is airtight except for the new attic stair I installed. The roof rafters are 2×6 on 16 centers with solid plywood sheathing and are in good shape. This doesn’t leave me a lot of space to create an R-30+ assembly at the roof. Minding my budget, the highest R-value I can get with a reasonable combination of 1″ of closed-cell and 4.5″ of open-cell spray foam is probably about R-23. That is unless I start adding insulation to the underside of the rafters in a perpendicular pattern. Now we’re talking a lot of extra expense! I’m not saying it wouldn’t have a return just may be more than I can spend currently.
My other option would be to keep my original design of installing the new air handler in the current building envelope below the attic ceiling and simply add insulation (and air seal around penetrations etc) to the attic floor. Likely I would blow in cellulose fiber and that would cover the ductwork to some degree…and yes I’ve read from Martin that I have to be careful about that approach as well in terms of condensation on the ducts.
还有其他的好处将信封to the roofline. We’d get to use the attic as a more climate-controlled storage space and it would be less of a concern about the air-sealing of the penetrations to the upstairs ceiling drywall, etc. But my question is, how is the best way to evaluate the effectiveness (purely in terms of impact to heat gain/loss) for each of these approaches? Option A being the “move the envelope to the roof” approach and option B being to add insulation to the attic but leaving the envelope where it currently resides at the drywall ceiling?
I’m a degreed mechanical engineer so maybe I’m overthinking this. My career has been primarily in the manufacturing and machinery side of the discipline. Hit me with the technical as much as possible – while I may be a bit rusty on heat transfer equations and such, I know I learned it at one point
Thanks in advance for any replies!
Matt H.
GBA Detail Library
A collection of one thousand construction details organized by climate and house part
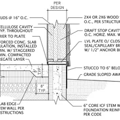
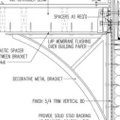
Replies
Hi Matt,
I am in the Atlanta metro and recently invested in some upgrades to my circa 2006 townhouse. As part of the project, I decided to have the inadequate cellulose insulation vacuumed out of the attic (an allergy and air quality issue) and replaced with spray foam applied to the underside of the sheathing. Initially, I wanted to spray a combination of closed cell and open cell to mitigate moisture concerns. I also had a target of R-38 for the total r-value.
I could not find a foam contractor who would bid the project as spec'd. They would only give me an estimate for R-30 of open cell. It was very frustrating. I eventually emailed a GBA contributor who also lives in this area and was advised that R-30 is sufficient for our climate. (This is what all the foam contractors work off of when putting together project estimates.)
To address potential moisture issues, I focused on additional air sealing to mitigate the stack effect. I also added a supply duct in the attic and installed a wireless moisture meter that alerts when whenever conditions are above 85 degrees and/or 50 percent humidity. So far this compromise seems to be working out fine. You may find it easier to complete your insulation project if you follow a similar strategy.
FYI. You are not limited to the rafter depth when spraying foam, but you do want to make sure they spray enough to give you the requested R-value. My experience is that spraying foam is a very competitive business. That said, I would focus on finding the best contractor even if he/she is more expensive. The last thing you want is a bad (and smelly) foam job.
Joe Lstiburek evaluates the two options you're contemplating here:https://www.buildingscience.com/documents/insights/bsi-074-duct-dynasty
Thanks to both for the replies. The article from Joe Lstiburek was quite helpful and sent me on a hunt for sure. It seems like I’ve read every article published by GBA and BSC on the subject in the last week including their many comments and replies. At least I know I'm in good company that this is not a simple thing to tackle as a remodel. If the roof shingles weren't only two years old (replaced before I purchased the house), I'd simply go with exterior insulation over the existing roof sheathing, seal off ventilation channels, thereby conditioning the attic and be done with it.
So to keep it short even at the risk of poor advice, I’ll jump right to it. After all the reading I’ve decided to “cathedralized” and condition the attic into the envelop. While closed-cell spray foam applied directly under the sheathing is touted as an almost fail-safe method (when properly applied), I’ve read enough concerns that I’d like to avoid spray foams as much as possible.
I’ve come up with a design that keeps the attic vented using polyiso rigid insulation boards for site built ventilation baffles and the cut-and-cobble stack of pancakes method in between the rafters. I'd follow that with a continuous layer of polyiso underneath the rafters for a total of about R-30. While a good majority of my rafter bays (76% by square footage under roof of the attic) have a straight shot from soffit to ridge for airflow, unfortunately, the other 24% are obstructed by a valley rafter. Is that 24% figure of unvented area over a magic threshold (if one exists) that I’m just asking for trouble with moisture problems since it won't be effectively vented? I think Martin would probably tell me 1 in 4 odds is too high.
If I go with the unvented approach, I’ve seen no real design solutions that don’t include spray foam as the primary means of creating the necessary air/vapor barrier under the roof sheathing.
The "unvented" cut-and-cobble method for which others have tried to advocate before (always losing), has the risks associated with eventual failure of the airtight installation method (spray foam around the edges or caulk, etc.). In my studying up, I did wonder if anyone has tried this method using an acoustical caulk at the edges of tight-fitting rigid foam between the rafters immediately under the roof sheathing. The primary failure mode of typical caulk is that it dries out and cracks, creating a pathway for air and therefore moisture to cross to the cold surface of the roof sheathing. Since acoustical caulk is designed to always stay flexible, seems like it would always remain as an effective air/moisture barrier in conjunction with the rigid foam.
所以飞机降落,我的发泄方法强g polyiso sound like it would work or is it doomed to failure since my roof is not effectively 100% vented? Is there a method of creating an unvented-cathedralized-conditioned attic that doesn’t use spray foam that perhaps I’ve not been able to find? Should I just give up on my ideals for avoiding spray foam entirely and bite that bullet since its likely my lowest risk option? Or should I perhaps seriously consider a hybrid solution: closed-cell spray foam on my unvented sections and the polyiso on my vented sections?
Thanks again!
Matt H.