Cost-Effectiveness of More Attic Insulation

My question, details below: is it worth adding additional depth to my attic insulation, given the realities of my old house.
I have a 1910 single-story (+partial basement) basic rectangular home with gabled roof. Lath and plaster, no wall or attic insulation, etc, etc. When i moved in, I can-foamed every opening I could find from both the attic and removing all fixture covers (the basement is finished so I can’t access most of that. I added the recommended vent area in the soffits (roof already has gable vent + ridge venting), and weatherstripped all the doors/windows. Location is central Idaho (Hardiness zone 6b and 7a)
Realistically though – it’s still as leaky as they come, and still un-insulated on 5 of its 6 “sides”.
上周,我终于吹的左右attic (you may have heard – it’ll be a heat wave next week, 112degrees – ouch). I went cellulose (less hazard to me, more environmentally friendly, I understand it shuts down convection better), but supplies were scarce, and i was only able to get~6+ inches在。这是理论上的地方between R10-R20
With the hard work behind me (adding the rafter vent channels), I’m now wondering if I should do a 2nd round to bring that depth up to R30-40, given that it’s out of scope in the near future to do a major retrofit to fix the other 5 faces of the home (eg replacing windows, and sealing & the walls, floor joists, and foundation wall)
I’ve struggled to find data-backed opinions here – help??
GBA Detail Library
A collection of one thousand construction details organized by climate and house part
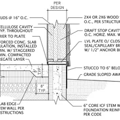
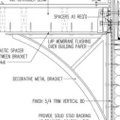
Replies
The heat loss through one surface is independent of the heat loss through other surfaces. So the cost-effective level of insulation for the attic is independent of how well-insulated the rest of the house is. What the cost-effective level of insulation is for the attic depends on a lot of factors that we won't know -- your cost of insulation, the value you ascribe to your labor if you're doing it yourself, your cost of heating, your cost of capital, how long you intend to own the house -- so it's impossible to come up with a one-size answer. But you can't go wrong with code-minimum for your area.
The related question is what is the most cost-effective improvement? Where do you get the most bang for your buck? Again that's hard to answer, but the general approach is to air-seal the entire house and add insulation where it can be done easily.
Thanks for the reply. I understand the heat loss (all other factors equal) is mostly independent between modes.
There are two parts to this reasoning, as i see it:
- first, since the loss is (mostly) independent between walls, ceiling, etc - are there any rules of thumb for ~ % loss by each surface for heating/cooling in *an uninsulated house* (my starting condition) in a similar climate? This would put a ceiling on my gains from attic insulation.
- second, are there other factors (such as extreme air leakage) that further limit the effectiveness (sticking with lack of sealing, say limit air-permeable insulation?
Taken together, these mean that adding X% more R-value in the attic adds diminishing returns ... I"m hoping there are some combination of experience, examples/cases studies that could be linked, or just rules of thumb that can help me understand what sort of extra benefit i could get with more insulation. It's not free or trivial to do - but neither does it cost a ton or take more than one long morning.
The problem with doing an energy retrofit on a house like this - at least prior to covid - my numbers had it much more economical to just tear it down. The studs are fantastic old-growth lumber, and we enjoy the oldness (Even found a lady's party invite card from the twenties in the wall) ... but literally everything else is counter productive to making an energy efficient house, from the foundation on up...
"are there any rules of thumb for ~ % loss by each surface for heating/cooling in *an uninsulated house* (my starting condition) in a similar climate? This would put a ceiling on my gains from attic insulation."
The ceiling on gains is the amount of heat you're currently losing through the attic. Percent of loss is the wrong lens to be looking at. Let's look at some real round numbers for the sake of example. Let's say your house currently costs $1000 a year to heat, and 25% of the heat goes out through the attic and 75% through the walls. The most you can possibly save by insulating the attic is $250 per year. But insulating the attic doesn't make the losses through the walls greater. So where you decide to stop with the attic is the same whether or not you also insulate the walls.
GBA tends to focus on offering practical (but science-based) advice. But I’m not sure what you are after here. You say your on research suggests the home is not going to deliver a reasonable return if you sink more funds into energy updates. Or am I misunderstanding your last sentence?
What are you after? Greater comfort? Lower energy bills? Saving the home because you are emotionally attached to it?
Saving an existing house rather than knocking it down and starting fresh is certainly a "green" thing to do in many cases, and I would think especially so in the case of a house old enough to be made of old-growth timber. That's certainly the way I feel about my 1901 house.
I agree with in concept; and FWIW my wife and I love the actual building, built-ins and details. Since I have lead-blocked it, had suspect areas tested for asbestos, and installed a central vac venting to the outside, we have no concerns about raising the kids in it while they are young.
However, a balance has to be struck and having "saved" two similar houses (full-gut, but not enlarged substantially, and NO lift/new-foundation needed) the cost difference will likely be very large, eating our solar budget, etc.
Further: realistically / unfortunately about all that could be saved is the wall framing itself - no roof / rafters, most lathe removed, siding removed, foundation replaced, all mechanicals replaced ... so the _actual_ difference in embodied cost for the "remodel" versus "teardown" isn't AS different as it would seem at first blush.
if only there were a machine that would rip the small 'lathe' nails out of the studs, they would be fantastic to re-use. I am totally blown away every time i deal with the old-growth construction.
RE: Knapp - Our goal is to eventually have an energy efficient house. The existing structure would required going all the way to bare studs amd floor joists) to seal and insulate sufficiently (not to mention when going to all that effort, retrofitting earthquake etc), installing new windows, etc. Its unlikely the finished product is cheaper than new construction (absent today's spike in lumber obviously) AND the results will be worse than new construction: no insulation under basement, on foundation walls, substandard earthquake resistance in foundation, etc. All of this disregards other benefits of new such as full (instead of partial 7') basement.
And for in-place upgrades besides the attic would just turn into that full gut remodel as well: difficult and ineffectual to just cut/blow-in/patch the (2x4) walls; OK so re-side with/~XPS.... But then we would definitely do the windows...
So I was referring to how its probably just the attic that makes sense, as I see it, today, until we can *fully* gut (or replace) the structure. Of course if there is something I'm missing... that's why I posted here of course.
One part of my question that shouldn't be as qualitative is regarding "air permeable insulation" -vs- highly leaky home
For my attic insulation, I did the best I could with spray foam but it is undoubtedly extremely porous, still. Do stated Rvalues of the blow in depending on stopping the bulk air movement? Arresting convection was one aspect that pushed me to cellulose over fiberglass, but I doubt its anything close to actually sealing...
所以我们同意有一个固定的X% loss (or $/yr) through the ceiling - how significant is that (affects the additional/relative improvement i can get by blowing in another 6 inches)
A 2000 sqft of R20 ceiling loose 2000/20=100 BTU per each degF delta, over 24h that is 0.024 Therms.
If you are around 6000 HDD in your area, you loose 0.024*6000=144Therm. If you gas is around $0.75/therm burned in an 85% furnace, that cost you $127.
Doubling the R value, halves this number so you save $65/year.
Central ID is either IECC climate zone 5B or 6B, depending on your exact location. Plant hardiness zones aren't particularly relevant. See:
https://www.steelbuildinginsulation.com/images/iecc-climate-idaho.jpg
A 6" layer of cellulose is way over R10. If raked smoothly & evenly, assume R20-ish at settled depth. That's a huge difference from ZERO insulation, and thick enough to be decently air-retardent. If it's left with thin spots and mounded high spots it won't perform nearly as well. During the cooling season the comparatively lower thermal diffusivity would make it perform substantially better at reducing peak ceiling temps than R30 low-density fiberglass, but during the heating season the advantage isn't quite as high (though still real enough.)
Whether it's "worth it" to take it up to R30 or R40 depends on your heating & cooling energy pricing, your projected time scale, and where you might otherwise apply that money. In most cases taking it to R30 or more on a DIY basis would usually be a no-brainer on a 10-15 year time scale (but do your own net-present-value accounting math.) Cellulose is cheap stuff, typically <$0.05 per R per square foot (at pre-pandemic pricing anyway).
@akos - that's really great info. I have some thermo background (but in SI units lol; obviously not the construction industry) - I will spend some time with these, if accurate it's a fantastic jumping off place.
@Dorsett,谢谢;看来我们跨越5&6 from your iecc link. The blow-in we used was rated at 3.5 R per inch. I discounted for several things: I'm no expert, I'm sure my application is a bit uneven. Also, there is actually some very old unfaced batting 14x14 "squares" spread in most areas (maybe ~1.5" thick ... someone put in a lot of effort for not much gain) - to be conservative i just discounted most of their contribution.
good info all; and assuming akos's numbers are realistic, i'll have to mull over ROI (likelyhood we do build/gut vs move; how comfortable is the house during next week's heat wave :) )
a question for all based on @dorsett's comment - I have a baseball field rake (~40" wide, light aluminum) - is "raking" blow in a thing? I would have assumed the compaction outweighs the benefits - is this worth doing?
>"I have a baseball field rake (~40" wide, light aluminum) - is "raking" blow in a thing? I would have assumed the compaction outweighs the benefits - is this worth doing?"
Raking it flat is ABSOLUTELY worth doing. The amount of "compaction" you will actually see is quite modest- less than the amount of normal settling that low-density blown cellulose experiences. (Think of it at "pre-settling" some of that.)
The additional losses of thin spots is quite large by comparison to the average losses. A thin spot of (6"-3" =) 3" on a 6" average loose fill is losing 200% as much as the average, whereas a high spot of (6" + 3" =) 9" is only improving the high spot's performance by 33%. The best overall performance is when the fill has perfectly even depth.
Blown cellulose will settle naturally on it's own, you don't have to do anything to it. It's not uncommon to use a rake to help get things a bit even when needed, but you don't want to over do it -- ideally you want to get a pretty even layer using ONLY the blowing machine to do it.
There IS a "shake and rake" fiberglass loose fill insulation product out there. This product is applied by shaking out the bag, then evening out the material with a rake. It works pretty well for small repairs and other odd jobs where it isn't worth getting a blowing rig setup. I've used this material myself when I only had a few small spots to insulate on a bay window I was reconstructing. It's a good product, but I wouldn't try doing an entire attic with it.
Bill
My guess is you could make much larger gains with more air sealing. You said this house has a partial second story that is a huge red flag enormous air leak where the second floor stops and the attic begins is all but certain in an old house and bordering on impossible to seal sell after you have insulated.
I have not done the math but if you got R22 in now and you wanted to get to R40 my guess is the payback time for the upgrade would be about 20 years.
These links maybe helpful
//m.etiketa4.com/question/devils-triangle-and-cathedral-ceiling-insulation
//m.etiketa4.com/question/devils-triangle-update
Walta
"much larger gains with more air sealing."
I don't see any real options for my situation - do you?
The workable options I'm aware of are best done with a full-gut. I do remember reading at some point of a (crazy-sounding) approach that ~tents the house, and presurizes it with a product that expands/bonds when hitting outside air ... I'm not sure if this was a real product, or an academic paper, and i can't find it online now; nor am I sure it applies to finished construction (versus a last step to catch small holes during new construction of a ~passive house level of detail)
Sounds like AeroBarrier:
https://aeroseal.com/aerobarrier/
It can be done in existing construction. It's popular in DC for multi-family dwellings since cannabis was legalized.
A plaster or drywall existing wall can be air sealed fairly easily using caulk and spray foam. Other surfaces might be more problematic. A lot of times old houses have wood floors with no subfloor or a plank subfloor and the whole thing leaks air. If the ceiling below is finished there's no way to get to the rim joist and seal it. You get a similar problem with wood paneling on walls or ceilings that don't have an air barrier behind.
Advocates of old wooden double-hung windows insist they can be sealed as tight as a submarine. That hasn't been my experience though.
AeroBarrier - that's it, thanks. A very interesting product. I reached out to a firm that apparently does it - i have a feeling the total cost to do existing would be quite high but it's worth looking into.
I have the floors you describe, of course, and i can't access many places, such as rim-joists/sill plates, the wall caps (too tight to get the foam in the right place) etc. If aerobarrier could seal all that robustly enough to last for a long time, that would be really interesting.
I do wonder about a few things: the long-term longevity of the bond / "patch" in the face of thermal cycles / movement / etc - seems like a bit of a fascinating mechanism; the safety in an occupied/finished house; and how much an old house like mine leaks through all the paces that would have to be covered prior to sealing - door/windows, kitchen areas... but all very interesting
Yeah, the first thing they teach you when you learn roofing or siding is "never rely on sealants alone." Houses move, sealants loosen.
It's a problem with all kinds of sealers, caulks and spray foam.
My non-quantitative assessment is YES, it's well worth it. I added ~R20 (6" fiberglass batts) to our house, which had old, nasty batts in the rafters with 3.5" of more recent fiberglass on top of the old stuff. We noted only a small impact on our heating bill, but the house has been much more comfortable in winter and summer. The comfort factor, alone, was worth far more than the cost of the insulation. It's colder where you are; I can't imagine that you won't notice the difference in both comfort and heating bill between R2o and R40 in your attic. Insulation is relatively inexpensive; it may not be the "most cost effective", but it's still a solid investment and a lot easier than some other improvements. You'll likely do it sooner or later, so why not do it sooner?
And the thing to remember is that once you get past the point of keeping your pipes from freezing -- 40F or so -- heating is only about comfort. And comfort can be hard to quantify beyond thermostat setting.
well, I now have a _small_ sampling of daily consumption data before/after adding the ~R20 cellulose discussed above. Thermostat schedule and general behavior has not changed.
On the positive side, there is a significant increase in comfort (important as we both WFH); the HVAC is able to keep up with cooling through about 5pm. The inside temperature ends up peaking at 79~80 (higher than is comfortable) on a 100 degree (90deg average) temperature day.
On the negative - energy use not reduced (in summer). The indoor temps achieved are obviously still not ideal, and as the cooling system is outpaced by the demand, the actual energy savings are ~nill looking at the utility hourly data compared to pre-insulation and similar temperatures. Eg, the AC was running at max duty cycle previously, and remains so all afternoon. I did notice that on less-hot days (max below 100), the AC was able to stop cycling on after about 9:30pm, which would imply some energy savings.
So, i'm probably going to take some additional action, but i have also broadened what i'm considering:
- white elastomeric paint over the south facing roof (we're a ~rectangle with a single simple east/west roof line, one hip (east) and one gable (west) end; black asphalt shingles).
- white paint on southern wall of house
- grid powered attic fan (have gable vent, continuous ridgeline vent, approximately 50% of the target net free area in soffit vents, and a solar attic fan)
Any other relatively easy options I should consider? Preferably diy-able (for an experienced person) in a day or two.
这听起来像是你还到我所说的“losing the battle" zone, which is where your A/C can slow the temperature rise, but can't reverse it or stop it. I suppose stopping the temperature rise without reducing it would be a truce, but that's a different thing to consider :-)
You won't see "energy savings", in terms of reduced energy use from an A/C that doesn't modulate. What you'll see is shorter cycles, or fewer cycles (fewer cycles is better than shorter cycles, but you'll likely have a mix of both). If you integrate these intevals of running over the day, fewer/shorter cycles means less total on-time which means less total energy consumed. If you can reduce your heat gain by 50%, and you reduce your A/C's on time by 50% as a result, you have a 50% energy savings. The A/C will still draw the same amount of current while running (that particular parameter is a function of the pressure of the refrigerant, which depends on the temperature of the condensor coil outdoors).
White paint DOES help. I have actually done this on commerical buildings before and it results in a measurable (since I had to measure it) improvement. You don't need fancy paint, either, you just need something white, and something that is compatible with whatever you're applying the paint to.
An attic fan may help you, but you'll want it on a thermostat (a common option), so that it only runs when the attic is too hot. You may want to try increasing the intake area of the soffit vents first if you can.
Radiant barriers can sometimes help here too, and are cheap and install quickly. You don't need the foil bubble stuff -- just the metalized film that is a radiant barrier only without any air pockets. This can be tacked under rafters and can help in some situations. Remember to consider ventilation though -- you don't want to seal up the spaces between rafters and create moisture traps.
Bill
yeah, I'm inclined to agree. since it's realatively low effort / one morning, and just a couple hundred $$, i might
- rake / push a little snugger into eves the insulation i have
- add another 6 inches
call it good :)
appreciate the help, it's an interesting learning process; tons of options.
Something that's worked really well for us is external blinds. We have 4, 8' wide roll-up blinds that we got from Costco (like $60 each), that we attached to the eaves of the house. These shade windows and the house wall on the S and W sides. The blinds are somewhat transparent so you can see through them (but it's not great) and they let light in. We use the blinds as needed; the W are down almost all summer, and they're all rolled up in winter. External shading of walls and windows is very common in the tropics and it can make a remarkable difference.