好的框架墙和屋顶北佛罗里达吗?

My architect thinks we should stick with conventional wood frame construction over ICF for reasons I don’t need to go into here. I’m struggling thinking of a good, durable wall for my climate zone if we decided to use wood framing for our walls.
I’m in climate zone 2. I like the idea of rigid foam even though I don’t really need it, but is it worth it? It seems like it complicates exterior finish details. The house will be stucco downstairs and siding upstairs. Should I have 1″ of rigid foam to eliminate thermal bridging or just forget it since my climate is warm enough to not need it?
I like Zip sheathing because the WRB is up at the same time the sheathing is up and it seems to be a well regarded product. I also like the idea of open cell spray foam to help air seal, assuming the installation is done properly.
This leaves me with:
Drywall
2×6 stud cavity with OCSPF (or another recommendation)
Zip sheathing
硬质泡沫塑料/ t + / - 1”he sheathing
Ventilated air gap (delta dry under the stucco or furring strips under the siding)
Stucco (lower floor) or fiber cement siding (upper floor).
Any changes to make it better? I’m open to anything. I’d like to get at or above R-20 even though code is only R-13 I think.
I’m having a similar dilemma with the roof.
So much on this site and so many of the Q&A’s are northern climate focused it makes it hard to figure out what is best for my hot humid climate!
GBA Detail Library
A collection of one thousand construction details organized by climate and house part
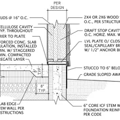
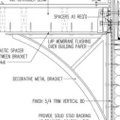
Replies
IRC code min for zone 2 is 2x4/R13 with no continuous insulation. If you use metal-lath hard stucco with a vent gap between the sheathing & lath you'll have whole-wall performance of about R10, after accounting for the thermal bridging.
If you bump that up to 2x6/R20 16" o.c. it'll be about R13+ whole-wall, but if you go to 24" o.c. stud spaceing it'll be close to R15. That's 33% less heat gain/loss than code min. An alternative solution would be to use R6 Zip-R sheathing and 2x4 framing, which will come in at about R15-R16 whole-wall. R6- Zip-R and 2x6 24" o.c. framing would hit ~R20 whole-wall, and would be easier to manage than the 1" foam on the exterior of the sheathing.
If you read the first chapter and look at Table 2 p10 of this document, you'll note that R15 whole wall is where you have to sharpen the accounting pencil to see if going much further is really financially rational. It may be better to spend the insulating sheathing money on PV solar for the roof &/or better windows, or exterior window shades etc. With R20-ish whole wall the window fraction starts to dominate the heat loss numbers, not the wall area. Heat gain is almost ALL from windows, with some roof gains.
Hot, humid? you should consider cellulose. Dense pack in your 2 x 6 walls will give you 50% over code. Raise heel truss, vented attic can be blown to R40 with ease. Good overhangs to keep the sun off the walls. Thermal bridging is more a cold climate concern so I'd be inclined to omit the exterior foam, as you note your biggest issue is topnotch airsealing and dense pack cellulose is excellent for that, also provides some thermal mass and humidity buffer. Ventilated rain screen for a reservoir cladding like stucco is essential, also a good idea under the siding.
As far as the roof goes, we definitely don't plan on a vented attic because there is going to be HVAC equipment in the attic. So for the roof I was thinking of having an unvented attic but a vented roof deck using furring strips or baffles or whatever technology is appropriate. I want metal roofing but asphalt shingles are still a possibility.
As far as the Zip-R sheathing, the only thing(s) I had a concern about was first, do you lose structural soundness by having a foam layer between sheathing and studs and second, isn't it backwards (shouldn't the foam be on the outside to protect the OSB?).
What about a 2x6 or 2x8 plate with 2x4 staggered studs?
Nick,
In a hot, humid climate without any risk of ice dams, there is no real reason to include a ventilation gap under your roofing.
If you want to create an unvented conditioned attic, you may want to read these two articles that list a variety of ways to insulate a sloped roof assembly:
Creating a Conditioned Attic
How to Build an Insulated Cathedral Ceiling
For more tips on designing a house for your climate, you might want to readHot-Climate Design.
Martin,
Despite not having a risk of ice dams, wouldn't a ventilation gap at the roof deck improve the durability of the decking? What if it is spray foamed underneath, won't that prevent inward drying?
Nick, Dana Dorsett is offering sound advice in the question of thoughtful allocation of your resources. In your climate zone you can afford to stay away from the complexity of fancy framing techniques like staggered stud layouts designed for much harsher climates. Your first priorities should be the appropriate sizing, shading, SHGF and orientation of your windows along with correct solar orientation of the the house as a whole. Your next priorities would be good air-sealing, HVAC and ventilation strategies (glad to see you're already have this in mind for your attic ductwork, although distribution strategies that keep all HVAC out of the attic entirely would be even better). Once you have all these squared away go for the simplest wall construction that meets your R-20 ish goals, either 2 x 4 with external foam board or 2 x 6 dense pack and save your pennies for some nice shiny PV bling on your roof.
BTW, structural insulated sheathing products (SIS) like the Huber R Zip have been thoroughly engineered and tested for the application. We've used them a couple of times and have had no problems. I'm more inclined to the 2 x 6/dense cellulose solution myself because of the overall lower environmental impact and the degree of thermal and humidity buffering it provides. But either approach is going to give you a well-performing PGH.
Martin, echoing Nick's comment on the vent gap but from a different angle, it has seemed to me that providing a ventilated cavity below the sheathing would have the effect of reducing the Delta-T across the insulation in conditions of full summer sun exposure when the decking material in contact with the roof covering can reach far higher temperatures than external ambient. Do you know if this hypothetical has ever been tested?
James,
Bill Rose has tested the hypothesis extensively. The temperature of the sheathing near the eaves may, in fact, be cooled by air flowing through a ventilation channel. But on the upper half of the roof, the air has gained so much heat that it is no longer able to cool the sheathing significantly.
If anyone wants to install this type of channel in Florida, the lower level of roof sheathing should be radiant-barrier sheathing with the shiny side facing the ventilation gap. This will add about R-2 or R-3 to the roof assembly R-value.
The problem with using exterior air to dry a damp building assembly is that in Florida, exterior air is usually more humid than interior air.
Martin,
What about drying? What should either be done or avoided assuming I need a conditioned attic? Seems like everyone puts spray foam under the roof deck here.
Nick,
I prefer to see thick rigid foam above the roof sheathing rather than spray foam under the roof sheathing. Options include SIPs, nailbase, or site-assembled rigid foam.
That said, I wouldn't worry if I were you.
In your climate, there isn't any reason to worry about moisture accumulation in roof sheathing that has been insulated on the underside by open-cell spray foam. Moisture accumulation in roof sheathing is a cold-climate problem, not a hot-climate problem.
In Florida, the air in your conditioned attic will usually be cooler and dryer than the exterior air. This type of roof assembly should be designed to dry inward.
in hurricane zones it's better to avoid the ventilation gap, since that increases the upward force on the sheathing at high wind speeds, making it more likely to lose the roof. Splitting the difference with some of the insulation under the roof deck with the rest above the roof deck is just fine, and using at least 3" of open cell foam on the underside of the roof deck should seal the rafters/trusses to the roof deck fairly well, and lower the thickness of the exterior foam requirement. You could also air-seal with caulk and go with damp-sprayed cellulose on the interior if you prefer (though I expect there are more foam installers than cellulose installers in your neighborhood.)
IRC 2012 code-min is R38 between 2x12 rafters or joists, and an R38 SIP or stacked up exterior foam is pretty fat. But R15 on the interior with R15-R20 over the exterior thermally breaking the rafters would outperform code min in most roof designs due to the much lower thermal bridging, and is an easier & cheaper build than a fat SIP or all stacked exterior foam solution. The limits of relatively easy building with stacked exterior foam is 5-6" thickness, after which the screw lengths are unwieldy making it hard to hit the rafters (and long timber screws get to be pretty expensive too.) Installing 4" thick exterior EPS + nailer deck (R16-17-ish) or ready-made 4-4.5" polyiso nailbase panel (R20-ish) is dead-easy, and you can fatten out the R on the interior with open cell foam or damp-sprayed cellulose or whatever.
If you follow Huber's fastener spacing & length recommendations for ZIP-R there isn't really any structural concern. The inch of foam on the interior is being pressed to the framing for high friction- and even if you lubed that interface with acoustic sealing caulk the 1" isn't much of a moment-arm. Yes, the foam is on the "wrong" side of the sheathing to protect the sheathing from the moisture drives of the stucco, but the product is engineered to take it (it's designed to work as weather resistant barrier for most wall stackups after all), and in combination with a top/bottom vented air space between taped ZIP and lath as a capillary break and steady moisture purge it will do just fine. For stucco clad assemblies Huber recommends a layer of high-perm felt or a permeable housewrap between the lath & ZIP, independently of the depth of the rainscreen gap:
http://www.huberwood.com/assets/user/library/L-3-ZIP_WALL_ISO-HC_STUCCO_AT_SOG.pdf
http://www.huberwood.com/assets/user/library/L-1-ZIP_WALL_SECTION-HC_STUCCO_AT_SOG.pdf