极barn insulation

Hi all I’m in the middle of building my new pole barn and was hoping to get your advice/thoughts.
First, the building design parameters:
– NY/Climate Zone 5A
– Building is a barn/garage/workshop/kids play area
– 36×64 building, 2×8 post construction, posts 8′ OC
– 1″ continuous closed cell spray foam has been applied as a vapor barrier through all walls of the building, sealing all gaps in the metal siding. (side note – Martin’s article recommends not using spray foam because it’s too hard to replace a siding panel – I replaced a foamed siding panel and it peels right off). I found the spray foam to be very affordable compared to house wrap (about 2x the cost)
– 24″ 2″ XPS (R-10) slab edge insulation is currently run on interior of the building to eliminate posts as a thermal break. Concrete will back to this and XPS aligns to the edge of the wall surface.
WORK NOT DONE YET:
– unheated floating slab will be poured in the next few months
– 1/2″ plywood interior walls on 2×4 horizontal members
– internal insulated ceiling (~R-50-60 blow in fiberglass or mineral wool) with plastic liner to be installed after concrete
– Building will be heated/cooled by a water-air GSHP, currently thinking 5 or 6 ton system w/methanol and fabric ductwork hung from ceiling.
Yes, I’m going a bit overboard on some stuff and yes this is better insulated than most houses.
Here are my questions for you guys:
1. I’m getting a bit mixed up on vapor barriers and condensation in the wall cavity. My plan was to use R-19 faced batt insulation in the wall cavity (to make the walls ~R-26), but I am concerned about creating a condensation trap and/or inadequately compressing the R-19 in the wall cavity and allowing excessive air/heat movement in the insulated space.
2.I’ve decided that under-slab insulation isn’t really needed in my application. Cost/benefit doesn’t seem good enough with unheated slab and it seems I get more “bang for buck” with vertical slab edge insulation. However I could definitely strip off another 1″ of material in the building and install R-5 board if it would make a big difference.
3. Some of the research I’m doing shows plastic sheeting used as a vapor barrier under the metal ceiling panels and on the interior face (behind plywood) of the walls. I don’t think I need this in the walls, but I think it would be valuable on the ceiling to create a completely tight space.
Any other suggestions are appreciated.
I have a thermal camera and energy simulation software and will validate whatever work I do once it gets cold.
GBA Detail Library
A collection of one thousand construction details organized by climate and house part
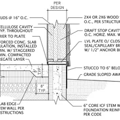
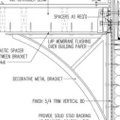
Replies
Hi Rich.
I don't have a lot of knowledge about pole barns, but I know that you don't want vapor-impermeable materials on both sides of your walls. When you do that, the walls cannot dry when they get wet. So, if you already have closed-cell spray foam installed against the back side of the metal siding, you should probably go with unfaced fiberglass batts and let your walls have the ability to dry to the interior.
Compressing larger batts to fill the uneven surface of the spray foam is a good idea. With the spray foam, you already have an air barrier, but to make the most of the fiberglass insulation, it can't hurt to detail your drywall as an additional air barrier. You also should air seal the top of the wall cavity, where it meets the unconditioned attic, if that wasn't taken care of with the spray foam.
If you have a vented attic space above your ceiling, you can install interior poly sheeting as a vapor retarder and air barrier, but you don't necessarily need it--there are other ways to make your ceiling air-tight, with airtight drywall for example, or with a variable perm vapor retarder.
Hopefully someone who has built a structure like this will see your post and offer some advice from their experience.
@brian
Thanks for the great feedback.
So...if I understand correctly you are recommending using unfaced R-19 batt for the wall cavities?
I'm getting a little confused by your second paragraph...you mention detailing the drywall as an additional air barrier - what do you mean there? Are you referring to installing a layer of plastic sheeting on the inside of the structure or using faced-batt insulation? Sorry if I do not understand.
Good point on the top of the cavities, those are air sealed with foam.
You are correct, I have a vented attic space. I installed baffles throughout. I will use the interior poly sheeting as you suggested.
Thanks!
Hi Rich.
I am suggesting unfaced batts in the walls covered with drywall installed to be airtight:How to Hang Airtight Drywall. You do not want an interior vapor retarder with a flash coat of spray foam in the walls.
Your 1" of SPF is around R6, which based on your climate provides condensation control for about R14 of fluffy insulation. With a decent warm side air barrier you can push that a bit higher, the R19 batts compressed 1" work out to around R16 so that is not far off. Your wall should work fine.
The sub-slab insulation is more for comfort than energy savings. In the winter time, an insulated slab will feel former. Still not the barefoot level, but at least not cold. With new construction, provided the cost is not silly, I would put it in.
I would double-check your heat loss calculations. In my area (zone 5) a 2600sqft building with R22 walls and R60 attic losses ~11000 BTU through walls and ceiling. Add in some windows, air leaks and slab loss, still a far cry from 5 or 6 ton unless you are planning on keeping some large doors open in the winter.
@akos Thanks for the helpful reply. Can you possibly share the chart/table/figure you're pulling those values from for the R-6 spray foam? I've been looking for a technical resource on that and am unable to find it. Are you saying that it is OK to have faced R-19 batts in the cavity? And if so is it acceptable to install with the batts to the interior of the building?
Good feedback on the underfloor insulation. I'll consider the cost as we move closer to that.
Hmm, to be honest I was just guessing based on 2400 sf and an assumption of 500 sf/ton. My building is rather tall (20 ft or so clear height), so I'm coming up with about a 2.5-3 ton load before air infiltration through doors is considered. If we add a safety factor and consider air stratification we'd be at about 4 tons. The unit would be two stage. Thanks for the feedback.
Check the data sheet from the foam manufacturer. Most 2lb SPF has a LTRR of 5.5 to 6. SPF installers are notorious for quoting silly R values for the foam, once the blowing agent dissipates, there is nothing special about the material, the R value is similar as other foam products.
The craft facer on batts is a smart vapour retarder as such it can be safely used. What you don't want with this assembly is a true vapor barrier since the SPF against steel panels is also a true vapor barrier.
Tall building does increase the surface area of the wall, so more heat load, but you are still not talking 3 ton range. Just run your building through one of the online calculators. Except for the garage doors, your building should be pretty air tight, infiltration loss should not be that much.
With a leaky building stratification can increase the stack pressure which would increase the load, since your building is well sealed, it won't increase your load much if any.
With a tall building just means that you need proper duct design to avoid stratification if you have any living space up high. This is easy enough to handle.
Thanks @akos
Yes in my experience I just run with the R-5/in assumption for any foam product. Anything else is just a nice bonus. I'm always a little surprised when someone tells me they get R-7.5/in from a foam.
Agreed, duct design is going to be key here. Might need to use HVLS fans (Big Ass Fans) in some areas for destratification.
I'm getting about 28000 btu/h heat load before infiltration and ignoring thermal bridging in my walls. Not sure of what ACH value to use for infiltration yet, but I'll just roll that into an arbitrary 25% safety factor and then increment to the next unit size. I have a 14x14 insulated overhead door and windows which have yet to be installed. Worst case ambient here is about 2 F, and worst case EWT (entering water temp) is about 32 F with the way I'll be building the ground loop. 28,000 btu/h with 25% safety factor gives me 35,000 btu/h. There will also be an antifreeze derate and a derate for low EWT. So, 3 tons would probably work, but 3.5 or 4 ton two-stage would be safe and allow a quicker warm-up/cool-down. 5-tons would be great for a quick warm-up/cool-down if I don't want to heat the structure as often.
I think you will get more suggestions on the garage journal forum under “General Garage Discussion” you will find a lot of experience there.
https://www.garagejournal.com/forum/
It sounds like you have put a lot on money and effort into turning your barn into a real building. I have to wonder if the pole frame saved you any cash by the time you fix all the problem the frame creates.
Be careful not to oversize your AC you risk not having the unit run long enough to remove moisture from the air and you could be left uncomfortably damp forcing you to lower the temp.
It is very rare to see math that can justify the very high install cost of a ground source heat pump.
Walta
@Walter谢谢。我有了一些短小l, but I feel this forum is a little stronger in terms of technical knowledge for construction.
Yes, this is a very expensive and complicated project, and that's probably my own doing. To be honest I've found the construction method of the pole barn to be a lot simpler to understand than a lot of more typical stick frame buildings. When you actually look at it it's very easy to understand all potential sources of infiltration/air leakage/etc. The only problem is there is a lot less detail work completed for this kind of construction.
Thanks for your thoughts on the GSHP thing. A few notes on that...
1. We live in an area with no natural gas available. Combustion fuel options are oil/LP, both of which I don't particularly want to use.
2.我安装GSHP过去,我不要这个nk it's too expensive. When you combine the federal and state incentives you get approximately 60% or more of the cost back. I'd be looking at $5000 or less to heat/cool the building after incentives. I'd be happy to share the math on that I'm going off memory from a calc completed about 3 months ago. GSHP would be self installed using my own equipment, expertise and rental equipment as needed.
3. As for oversizing, agreed 100%. We would be purchasing a 2-stage GSHP which would help. However I think as noted in my reply to Akos above that we probably need to drop to 4 ton 2-stage.
Thanks!
What you think, guess, hope and wish are soft feelings. The answer to the hard math question of how many years will it take to recover the extra costs is a real number we can talk about.
If you have a BEopt model that shows a ground source system closest to the bottom of the graph I would like to see it.
https://beopt.nrel.gov/
Walta