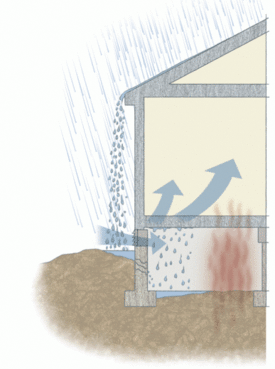
I’ve done a bunch of home weatherizing and insulating projects over the years; let me tell you about the worst.
By the mid-80s I had already done quite a bit to improve the energy performance of our house—a 1785 cape in Dummerston, Vermont—including gutting all the walls; insulating them with fiberglass plus an inch of Styrofoam insulation on the interior; and hiring a weatherization professional to caulk and air-seal most of the house. But when we would pick up our young daughter from the floor, she’d be cold to the touch. With our Vermont Castings Resolute wood stove cranking full-bore, the temperature at the ceiling in our kitchen living area would be well above 70 degrees, but it hovered in the 50s at floor level—where our daughter was crawling around. I had to do something.
What I did was insulate and air-seal the underside of the floor. This wasn’t so bad where we had a full basement—it meant cutting pieces of extruded polystyrene (XPS) to fit between the floor joists and against the underside of the subfloor, then wedging them into place. But about a third of our house, including our kitchen, has a crawl space under it instead of a full basement—and insulating that part of the floor was incredibly challenging.
My plan was to install the two-inch-thick XPS, leaving a quarter- to half-inch gap at the edges along the joists, and then seal those edges with expanding foam sealant, which would provide a good air seal. To access the crawl space from the basement, I first had to remove stones from the dry-stone foundation, creating an access hole. Then, because there was only about a six-inch space from the bottom of the joists to the floor of the crawl space, I had to dig a sort-of access trench to get in and move around.
避免项目好几个星期之后,我终于做nned a pair of old coveralls one sunny, late-autumn afternoon, put on a dust mask, and slithered into the cramped, dark space, trowel in hand. I have these vague, mostly repressed, memories of inching along under the kitchen floor, dragging an extension-cord-tethered light with me to illuminate the cobwebs and assorted wildlife that called our crawl space home.
After digging in far enough in my expanding trench network, I’d crawl back out to grab a piece of the insulation. I don’t recall how I cut the insulation boards to fit—whether I did that in the crawl space or out in the full-height basement—but I do remember it being really hard. It was especially difficult because every piece of insulation had to be a different size and shape. Our kitchen addition was built around 1800, and the joists are roughly ten-inch-diameter round beech logs. These joists were in remarkable shape, owing perhaps to the very porous soil, but the insulation had to be trimmed to fit around the bumps and bends.
Once the many insulation pieces were cut and fit—held in place with nails I think—I crawled back in with a polyurethane sealant foaming gun and a length of plastic tubing. This I used to foam-seal all the joints. The foam canister had to be held upside down when the foam was injected, and I awkwardly directed the foam into the gaps with the tubing. This particular phase of the project was particularly challenging—all the more so because polyurethane foam creates a real mess. If you get any on your hands or face, you basically have to wear it off. And I had to work fast, because the foam would begin to cure in the tubing.
So I wore goggles, along with my coveralls, and even a bandana over my hair—as much to keep out the spiders as the spray foam. But after a number of weekends of this (how many I no longer remember), I finally finished the job.
I report on this project not to scare readers off from weatherizing and insulating, but to make the point that the work isn’t always easy or fun or even safe. Some projects are really difficult and unpleasant—though I think in the annals of energy conservation few experiences could be worse than my crawl-space insulation project.
I also report on this to describe the incredible difference the work achieved. Starting immediately, the huge floor-to-ceiling temperature differential we had experienced was reduced to a much more reasonable level of maybe five to ten degrees. This house will never be as tight and comfortable as a new one that I would build today—a house that could be heated with a few 100-watt light bulbs in each room—but the work that I did makes our house reasonably comfortable and relatively affordable to heat. For a 235-year-old house, it’s really not too bad!
Our older daughter, whose cold little body inspired me to embark on this project twenty-three years ago, has now graduated from college (perhaps not coincidentally in a warm climate!). But the insulating and air sealing work I did in that crawl space benefits us to this day.
One Comment
polyurethane
Hmmm..... polyurethane sealant foaming gun: This is not a very sustainable material. It's made of oil, so it's not renewable. And in XPS the material that delays fire development doesn't disintegrate in nature. Reading you have sealed off everything, I hope the beams and panels of your floor are not made of wood, since they need good ventilation to avoid deteriorating. You also should cover the floor of the crawl space to avoid humidity as much as posible. You could do this with a PE foil.
Log in or create an account to post a comment.
Sign up Log in