Cladding a loft space in a roof with no ventilation

We are busy renovating a property built in the 1930s. As we go along we inevitably find things that are a bit surprising, forcing us to change our initial plans.
We would like to ask for advice on what the best course of action is to clad the upstairs area under the roof.
The situation
房子的楼上的地板下roof (loft space). Pretty standard with an additional small roof space above and small slope and low structural partition on the sides. It has been that way for many years. It is currently not insulated (with minor exceptions) and clad in a kind of fibrous boarding, which we will need to replace anyway due to the internal changes we are making.
And now for the bad and important bit: There is no ventilation in the roof space, which probably accounts for the mustiness and slight dampness on the inner paper lining under the (non breathable) roof felt and the mould growth if the windows are left closed.
There is no easy solution to providing ventilation. Under the eaves the external walls (granite cavity walls) are built right up to the roof. Diamond drilling air vents the whole way around would risk splitting the granite and be very expensive. There are no compatible venting tiles available that would match the tiles on the roof and as the roof space is lived in so you would need one for every channel. The best course of action – taking the tiles and battens off, adding insulation, replacing the felt for a breathable membrane, adding ventilation and re-tiling – is way out of our budget for the time being.
So given that we are living in an non-ventilated cold roof space (!) what is the best course of action to clad the space without amplifying the potential risk of condensation/dampness. Ideally we would want to do this in a way that leaves the option of replacing the roof in the future, without having to redo the inside of the space.
Is it a good idea to put a VCL in to reduce the amount of damp air going into the roof space/channels between the wooden beams? I assume it can’t make the situation worse! I also assume that putting in wool between the rafters is a bad idea at present as it would prevent the damp air going into the upper roof space, but maybe if we have the VCL this wouldn’t add to the existing risk? Go from bad to bad but less wasteful. Or use materials that can hold on to the moisture and regulate the environment until windows are opened, etc.
Our original plan of keeping everything breathable and as sustainable as possible (wood fibre and sheep wool insulation, etc) doesn’t seem to make sense when the outer layer isn’t breathable and would no doubt add to condensation risks.
Before everybody cries you have to bite the bullet and redo the roof, this simply isn’t an option at the moment (financially). So it’s how to make a bad situation live-able and if possible a little better.
Any advice greatly appreciated!
Kaspar
GBA Detail Library
A collection of one thousand construction details organized by climate and house part
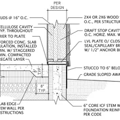
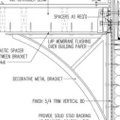
Replies
Kaspar,
First, some introductory points:
1. It's always a good idea to tell us your location or to indicate your climate zone, since climate can affect building specifications. I'm guessing that this house is in Europe.
2. Your use of the word "cladding" is confusing. I'm not sure whether you are using that word to indicate exterior sheathing or interior finish materials.
3. I have no idea what "VCL" stands for or means.
Now that I have mentioned these introductory matters, I'll address your questions. The house you describe would be called a Cape (or a Cape Cod) house in the U.S.
It's perfectly possible to build an unvented insulated roof assembly. If you are doing the work from the interior of the house, you need to install spray polyurethane foam insulation between your rafters. I'm not sure what type of roof sheathing you have -- whether solid boards, plywood, or skip sheathing. If you have skip sheathing, you'll probably want to install strips of cardboard or rigid foam between the rafters first, so that the spray polyurethane foam doesn't gum up the spaces between the skip sheathing.
For more information on creating an unvented sloped roof assembly, see this article:How to Build an Insulated Cathedral Ceiling.
Hi Martin, thanks for the quick reply.
Yes Europe. Windy location, quite exposed, near the sea.
Cladding - interior finish materials.
VCL - Vapour control layer.
Yes, working from the interior.
Had hoped to avoid polyurethane!
Thanks for the link,
Kaspar
Kaspar,
If you were building in the U.S., there would be no legal insulation approach other than spray polyurethane foam. The use of air-permeable insulation materials (fiberglass, cellulose, or mineral wool) between rafters is not permitted in the U.S. unless you have a ventilation channel between the roof sheathing and the top of the insulation.
In some European countries, building regulations allow the use of air-permeable insulation materials in unvented assemblies. You will have to check with your local authorities and local building experts to see if these methods are permitted in your country. Note that these roofs have to be detailed carefully, because the roof sheathing is at risk of moisture accumulation and rot if you get things wrong.
An American company that imports European building materials is promoting the use of fiberglass insulation in unvented roof assemblies. This approach is considered unusual in the U.S., so it is only being attempted here by brave pioneers. For more information, seeYes, Unvented Roof Assemblies Can Be Insulated With Fiberglass.
We do not intend putting in insulation between the rafters until we have ventilation. The risks here are the same as in the US! We just want to make the inside liveable while we wait until we can afford the bigger job, in a way that doesn't mean we have to do the inside again at a later date.
Kaspar,
A low-risk approach would be to install a continuous layer of rigid foam on the interior side of your rafters, followed by gypsum drywall.
The seams of the rigid foam should be taped with a high-quality tape to prevent air leakage. The easiest type of rigid foam to tape is foil-faced polyisocyanurate.