Insulating a cathedral ceiling conundrum ad nauseum

Even with the litany of information on this website et al. I am still perplexed by a situation.
Some Basic Info:
Climate Zone 5b
House type: 1-3/4 stories Cape Style with 2×6 roof rafters. 12-12 roof pitch at the front with an offset gable dormer and 5-12 roof pitch at the rear
We are in the process of an extensive whole-house renovation and decided that cathedral ceilings on the second floor will help make the otherwise compact space feel more spacious. The challenge is the roof rafters are 2×6 and increasing their depth will encroach on important living space, in particular at the 12-12 side where the staircase is being relocated.
I’ve considered vent shoots made out of 1″ rigid (per an article in FH) and closed cell spray foam to the underside, but still come up short on R-value.
Then I considered the Cool Vent Panel by Hunter panels with 2″ rigid backing over top of the tongue & groove sheating with closed cell spray foam underneath in the rafter bay, but then I became concerned with sandwiching sheathing between two high density foams and potentially creating compost.
Lastly, I’ve considered just 5″ of closed cell spray foam and hoping for the best. I don’t necessarily want to “hope for the best.”
With these circumstances, does anybody know the correct solution?
Thanks!
Ryan
GBA Detail Library
A collection of one thousand construction details organized by climate and house part
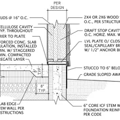
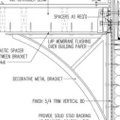
Replies
嗨,瑞安。
If you are considering the Cool Vent panels, you must have the option to work from the exterior. If that is correct, than why not install exterior rigid foam (you don't need to use a manufactured product like Cool Vent, necessarily) and fill the rafter bays with fibrous insulation like cellulose for an unvented assembly? I assume you read these articles, but they should give you all the info you need to make a decisions:
How to Build an Insulated Cathedral Ceiling
How to Invocs stall Rigid Foam on Top of Roof Sheathing
Will furring the rafters 1.5" -2" really affect your headroom so negatively that its not an option? This would allow an R49 unvented assembly. (Exact R value will depend on the brand of foam).
You could also contact your Building Official and explain your situation and see if they will accept a modification. R38 +- is still much better than what was there. There is an exception in the IECC that will allow R30 if the rafters do not offer enough space but it can only be a max of 500SF.
The exterior rigid retro fit is certainly an option(a really good option) but it will add significant cost/labor to the project even if you were planning on a new roof.
Brian and Jon, thank you.
对添加硬质泡沫塑料或通风降温panels to the roof deck, I'm still coming up short with the 2x6 rafters to install adequate air permeable insulation to achieve R-value. There is room to fur down the rafters at the rear; however even 1" at the front 12-12 would encroach on the headroom for the stair (see attached elevation). My building inspector has agreed that R 38 would be acceptable, though my question still begs: even with R38 closed cell HFO foam, will there be risk of moisture at the sheathing and/or will the shingles fail?
The collar tie shown in the elevation is not planned to be installed, however, I'm contemplating whether that actually makes more sense to install at this point and just blow in cellulose or batt insulation.
Closed cell foam installed directly to the underside of the roof sheathing (Hot Roof) is a standard installation method and will generally not void any shingle warranty or have adverse effects on the sheathing, assuming it is installed correctly. I'm sure there are many articles on GBA to explain this method.
With only the small area of sub-code headroom at the stairway you could simply fur all other portions of the cathedral ceilings to allow for thicker foam. Also, even if you furred the rafters over the stairway, the total area that would end up being below 6'8" would be so limited that I would think the building inspector would accept it to allow for greater insulation. There is always some wiggle room on existing structures as long as it doesn't affect life safety. Any normal inspector would be inclined to work with you to achieve the best end result if you take the time to consult them ahead of time.
>"My building inspector has agreed that R 38 would be acceptable, though my question still begs: even with R38 closed cell HFO foam, will there be risk of moisture at the sheathing and/or will the shingles fail?"
It won't fail, but you can't hit a full R38 in a 5.5" deep 2x6 cavity even with R7/inch HFO blown foam unless you over-fill and trim flush (a real PITA with 2lb foam), and it's pretty much a waste of expensive ( environmentally and financially) foam. At a more realistic 5.25" average depth (minimal trimming) it's between R36-R37. But the thermal bridging is woefully robbing that foam of it's true potential. Do the math:
https://www.finehomebuilding.com/2017/07/10/closed-cell-foam-studs-waste
But it's an environmental travesty when it's performance is being so under-cut, even with HFO blown foam:
https://materialspalette.org/wp-content/uploads/2018/08/CSMP-Insulation_090919-01.png
At 5"+ the foam itself is structural- you almost don't even care if the roof deck rots when the shingles eventually leak.
In zone 5B installing 2" of HFO blown foam (R14) and 3.5" of rock wool or high density fiberglass batt or 1.8 lbs dense packed fiberglass (~R15 for any of them) would yield nearly the same whole-assembly performance at about half the (environmental & financial) cost, with a much improved drying path toward the interior. Then when it's time to re-roof, adding a 2 inches of RECLAIMED (used) 2lbs roofing polyiso (or 1.5" of virgin stock 1lb density foil faced polyiso) above the roof deck would bring it up to code performance on a U-factor basis, and improve the resilience at structural roof deck by keeping it warmer and drier in winter.