Rigid foam, vapor barriers, and moisture issue avoidance

I am in process of picking 3″ of EPS product for under my slab, around my stem wall and exterior wall CI. I have read through posts on GBA and articles on the Building Science website such asherethat state the following is something to avoid, especially when using exterior rigid foam in your wall assembly:
“Incorrect use of vapor barriers is leading to an increase in moisture related problems. Vapor barriers were originally intended to prevent assemblies from getting wet. However, they often prevent assemblies from drying. Vapor barriers installed on the interior of assemblies prevent assemblies from drying inward. This can be a problem in any air-conditioned enclosure. This can be a problem in any below grade space. This can be a problem when there is also a vapor barrier on the exterior. This can be a problem where brick is installed over building paper and vapor permeable sheathing.”
So currently I am planning to use 3″ taped Type II EPS under my slab and 3″ of taped Type II EPS around the stem wall. We also plan to use two layers of taped 1.5″ Type II EPS on the exterior walls, overlapping the seams with stucco cladding. The build is in Yakima WA which is Climate Zone 5, which I’m told via local sources requires an vapor barrier for the exterior walls as well and possibly a vapor barrier under the slab.
To verify, should we be using unfaced EPS products in all three cases where we are using it? Based on the posts I see on GBA and Building Science I’m thinking the answer is yes.
If that’s true why do manufactures push faced products for all these applications (like here with insulfoam) like there isn’t a possible issue with it?
And lastly, if code requires a vapor barrier where is a safe place to put it and what should be used (I see references to interior latex paint being a solution in the Building Science article)? What about the slab?
GBA Detail Library
A collection of one thousand construction details organized by climate and house part
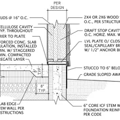
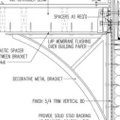
Replies
Joshua,
不幸的是,在乔Lsti语言burek article that you linked to is imprecise. Although Lstiburek talks about the risks of "vapor barriers" in the article, he's really talking about the risks of interior polyethylene, not vapor barriers.
Many types of rigid foam, including foil-faced polyiso and faced EPS, are vapor barriers. Properly specified, these rigid foam products are not risky. Moreover, polyethylene under a concrete slab is always a good idea -- never risky.
For more information on these issues, see these three articles:
Vapor Retarders and Vapor Barriers
Do I Need a Vapor Retarder?
Worries About Trapping Moisture
In your case:
1. Under your slab, you want a continuous horizontal layer of rigid foam. Above the rigid foam, you want a layer of polyethylene. Then concrete.
2. On your stem wall, the rigid insulation can either go on the interior side of the concrete wall, or on the exterior side of the concrete wall. The information in this article applies to crawl spaces as well as basements:How to Insulate a Basement Wall.
3. On your above-grade walls, any type of rigid foam will work from a building science perspective, although green builders prefer polyiso and EPS to XPS for environmental reasons. When an above-grade wall has exterior rigid foam, you don't want to install an interior polyethylene vapor barrier. For more information, seeHow to Install Rigid Foam Sheathing.
Joshua,
Before you finalize your decision to install stucco cladding, you may want to read this article:To Install Stucco Right, Include an Air Gap.
"...I'm told via local sources requires an vapor barrier for the exterior walls ..."
The only location of concern is the above grade timber framed walls. With 3" of EPS on the exterior of an insulated 2x6 framed wall wall it does NOT need or want a vapor barrier on the interior side, which would only prevent drying. In zone 5A you only need a minimum R7.5 on the exterior of 2x6 to meet IRC 2015 code without an interior vapor retarder, and at R12.6 (~R13.5 at temperatures that matter) you have nearly twice the code minimum. See TABLE R702.7.1 CLASS III VAPOR RETARDERS (about 1/4 of the way down the page):
http://codes.iccsafe.org/app/book/content/2015-I-Codes/2015%20IRC%20HTML/Chapter%207.html
At 3" EPS is a minimal Class-II vapor retarder even without facers at about 0.8-1 perm. Using EPS with facers won't change the drying capacity much unless you are forced to use 4-6 mil polyethylene (0.05-0.08 perms) on the interior. If you use only standard interior latex paint on wallboard on the interior it will run about 3-5 perms, which is still a Class-III vapor retarder sufficient to protect against wintertime moisture accumulation in the sheathing when you have R7.5+ on the exterior, but ~5x more drying capacity toward the interior than you would have toward the exterior through 3" of unfaced Type-II EPS.
If the locals refuse to be educated about the requirements of Chapter 7 of the IRC, use a smart vapor retarders such as 2-mil nylon (Certainteed MemBrain) on the interior, which is a Class-II vapor retarder when the moisture content in the wall cavities is low, but becomes vapor open if it's damp enough to support mold growth. I'll run you 12-15 cents per square foot, installed, probably 3x what it'll cost for 4-mil polyethylene, but it won't trap moisture.
Dana and Martin,
Thank you for the responses.
I know that a 3" Type II EPS is a good fit for the slab and stem wall based on previously addressed questions I have asked.
Based on your feedback it sounds like unfaced is a better choice for foundation rigid foam since it allows any moisture to dry out more easily than with a faced product?
For the exterior wall rigid foam is EPS Type II overkill in terms of compressive resistance?
我知道EPS是更容易破碎nd I would think facing and/or using denser types of EPS could helps mitigate any breaking of the EPS panels during the fastening/install process.
Any recommendations that differ for two layers of Type II 1.5" EPS on the exterior walls with these concepts in mind?