Wall and roof construction ideas

We’re hoping to build a house this summer. It’s the first time we’ve done a ground-up build, though we’ve remodeled and lived in a couple century-old homes. I’m looking forward to building a tight, efficient house, and to no longer heating with coal. I’d like to run my proposed assemblies, along with a few questions, by the experts here.
We’re building in Northeast PA, Climate Zone 5. I’m including an image of the house we’re planning to build. House is about 2700 sq. ft., and if we can button it up tight enough, I’d like to heat/cool with minisplit units.
BASEMENT
We’re planning on 10″ poured concrete walls, with 3″ EPS foam on the inside. Wall foam will extend down to the footer before the slab is poured, creating a thermal break.
2″ or 3″ EPS foam under the slab.
Sill area sealed with Triple Guard.
Rim joist area insulated with fiberglass insulation. Seams also caulked or sealed with spray foam if needed.
Oh, and an air tight sump lid
WALL ASSEMBLY (listed from inside to outside)
– 1/2″ Drywall
– 2 x 6 wall with fiberglass insulation
– ZIP system sheathing with taped seams
– 2 layers 1.5″ polyiso foam with staggered seams
– WRB housewrap
– Furring strips
– Vinyl siding
*windows will be “outie” windows, installed with plywood window bucks.
ROOF (listed from inside to outside)
This is the part I’m most unsure about. Our house has bedrooms and dormers in the second floor, so I think and unvented roof assembly with a conditioned attic space is the best option.
– 12″ fiberglass insulation in rafter/truss area
ZIP system roof sheathing with taped seams.
2 layers 2″ polyiso insulation with staggered seams
Roof Sheathing
Ice & Water shield (where needed), Roofing Felt, and asphalt shingles.
**Overhang will be constructed as shown in attached image (sourced from greenbuildingadvisor.com).
QUESTIONS:
In the wall assembly, should I use kraft-faced insulation? Or will I see a benefit from using a smart barrier such as the Certainteed Membrain?
由于邮政系统将我的主要空气巴里r, what is the best way to tape the windows into the ZIP sheathing? Should I just use a peel-and-stick membrane all the way from the ZIP sheathing, up to and over the front lip of the window buck?
Because of the construction of the roof overhang, I can’t tape the face of the wall sheathing to the face of the roof sheathing. What’s the next best option? Can I run the wall sheathing (and foam insulation) as close to the bottom of the roof sheathing as possible, then seal everything with caulk and spray foam?
Do I need a vapor barrier or air barrier over the fiberglass insulation in the attic?
GBA Detail Library
A collection of one thousand construction details organized by climate and house part
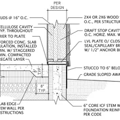
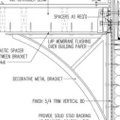
Replies
Foeller,
Here are my reactions.
1。”Rim joist area insulated with fiberglass insulation." This approach will only work if the exterior of the rim joist is covered with an adequately thick layer of rigid foam. I think you are planning to do that, although your description was a little unclear.
2. Your wall assembly is fine, except for the fact that most manufacturers of vinyl siding don't permit their product to be installed on furring strips. This may more may not be a problem, depending on your own comfort with bending the rules. Such an installation will probably void the siding warranty. For more information, seeCan Vinyl Siding be Applied Over Furring Strips?
3.在区5中,屋顶组装exteri相结合or rigid foam with interior fluffy insulation needs to have a minimum of 41% of the roof's total R-value in the form of rigid insulation. In your case, the fluffy insulation (fiberglass) has an R-value of about R-44, while the polyiso has an R-value of about R-20 (de-rating the R-value of the polyiso to R-5 per inch to account for polyiso's poor cold weather performance). That gives your roof assembly a total R-value of about R-64, with only 31% of the roof's total R-value coming from the rigid foam. So this assembly fails -- it doesn't meet the target (a minimum of 41% of the R-value must come from the rigid foam).
For more information on this issue, seeCombining Exterior Rigid Foam With Fluffy Insulation.
Foeller,
Q. "In the wall assembly, should I use kraft-faced insulation? Or will I see a benefit from using a smart barrier such as the Certainteed Membrain?"
A. Either product will work. Remember, the most important thing you can do to improve the thermal performance of your wall is to pay attention to airtightness at the time of construction.
Q. "Since the ZIP system will be my primary air barrier, what is the best way to tape the windows into the ZIP sheathing? Should I just use a peel-and-stick membrane all the way from the ZIP sheathing, up to and over the front lip of the window buck?"
A. You are planning to include housewrap, so you have to decide which of these two layers -- the Zip sheathing or the housewrap -- will be your water-resistive barrier (WRB). When it comes to flashing the windows, the location of the exterior air barrier is irrelevant. All that matters is the location of your WRB. Window flashing must be integrated with the WRB, not with the air barrier. The main disadvantage of choosing Zip sheathing as your WRB (compared to using housewrap as your WRB) is that you can't lap Zip sheathing -- you have to depend on peel-and-stick tapes for waterproof horizontal seams.
Once you decide which material will be your WRB, we can give you flashing advice.
Q. "Because of the construction of the roof overhang, I can't tape the face of the wall sheathing to the face of the roof sheathing. What's the next best option? Can I run the wall sheathing (and foam insulation) as close to the bottom of the roof sheathing as possible, then seal everything with caulk and spray foam?"
A. Yes, you can do that. Or you can build your overhangs after the wall sheathing has been sealed to the roof sheathing. For more on this type of "applied overhang," see this article:Airtight Wall and Roof Sheathing.
Q. "Do I need a vapor barrier or air barrier over the fiberglass insulation in the attic?"
A. In your climate zone, the building code requires a vapor retarder (not a vapor barrier)under, not over, the fiberglass insulation in the attic, unless you are installing exterior rigid foam, in which case ordinary latex paint is all you need.
If you have fiberglass insulation an the floor of a vented unconditioned attic, the usual way to meet the vapor retarder requirement is to use vapor-retarder primer (paint) on the ceiling drywall.
For more information on this issue, seeDo I Need a Vapor Retarder?
Martin,
Thank you for the quick response. As always, your information is so helpful and you mention a couple things that I hadn't thought of.
1. Rim joist area will be covered with rigid foam on the outside as well, so fiberglass on the inside should be adequate.
2. I wasn't aware of the issue with manufacturers not recommending vinyl over furring strips. We took this approach on our current home several years ago, and have no issues with it (other than the 100-year-old walls being a bit wavy to begin with). I would also imagine that the cheaper/thinner the vinyl siding is, the more likely it would be to have problems.
3.I read the article you referenced, and I'm not sure how I missed the 41% rule. So, if I'm calculating correctly, I would need either 12" Fiberglass (R-40.8) plus R-29 foam, or 10" fiberglass (R-34) plus R-24 of foam. Is it necessary to de-rate the entire foam assembly for cold-weather performance, or will that affect the outer layer more than the inner layer?
Window Flashing - Thank you for pointing out that I need to be mostly concerned with flashing into the WRB, which in my case will be the housewrap. I was looking at it completely from an air-sealing perspective.
Attic vapor retarder - I should have been more clear on this question. Part of the attic will be a conditioned unfinished attic space with insulation beneath the roof deck (basically on the attic ceiling, not the floor). Drywall installed in the 1st-story ceiling and 2nd-floor bedrooms will all be painted. But I'm concerned about air leaks carrying moisture into the conditioned attic space. I'm also told that if I install a vapor retarder inside the fiberglass insulation that I may be required to protect it with drywall for fire-safety reasons. What would you recommend in this situation?
Foeller,
Q. "Is it necessary to de-rate the entire foam assembly for cold-weather performance, or will that affect the outer layer more than the inner layer?"
A. That's an excellent question. The thicker the polyiso, the more lenient you can be with the de-rating. This is basically a seat-of-your pants determination, although it is ultimately based on measurements and math. (For more on this issue, seeCold-Weather Performance of Polyisocyanurate.)
It's probably OK to rate the outermost 2 inches of polyiso at R-4.5 or R-5 per inch, and the next 2 inches at R-5.5 per inch, and the next 2 inches (if you have 6 inches) at R-5.75 or R-6 per inch. Ballpark.
Q. "I'm concerned about air leaks carrying moisture into the conditioned attic space."
A. I assume that you are talking about air leaks into the space from the exterior. During the winter, these air leaks will bring dry air, not humid air, indoors. During the summer, these air leaks will introduce moisture into the attic.
Q. "I'm also told that if I install a vapor retarder inside the fiberglass insulation ..."
A. If your roof assembly is insulated with a combination of exterior rigid foam and interior fluffy insulation, you won't have an interior vapor retarder. The basic principles are described in this article:Calculating the Minimum Thickness of Rigid Foam Sheathing. (Although the article I linked to discusses wall assemblies, not roof assemblies, the same principles apply to this type of roof.)
Q. "I'm also told that if I install a vapor retarder inside the fiberglass insulation that I may be required to protect it with drywall for fire-safety reasons."
A. It's certainly true that kraft facing can't be left exposed, because it's a fire hazard. In any case, it's a good idea to have an interior air barrier whenever you install fiberglass batts -- so an interior layer of drywall is generally a good idea. The drywall is a good air barrier (and addresses any imaginable fire safety concern).
In zone 5 IRC code min for basement walls is now R15 continuous insulation, so a mere 3" on the interior isn't going to cut it.
It may make be cheaper to use minimalist 2" + 2" insulated concrete forms (R16.8), or 2.5" + 2.5", which would still give you at least 2" of thermal break against the footing, but also provides a modest energy use performance from the thermal mass of the 10" of concrete wall.
It's almost always going to be substantially cheaper to build with a vented attic using energy heel trusses than insulating at the roof deck, even if it means building a taller house to get rid of the dormers. Dormers are prone to being both snow traps and ice-dam starting heat leaks, and complicate the air sealing and roof waterproofing. Maybe they look cute, but they're really not a great idea when going for higher performance in new construction.
For a bunch of other zone-5 specific ideas, even though it's targeted at retrofits, it's worth looking through the Mass Save Deep Energy Retrofit Builder Guide (developed by Building Science Corp for a program in Massachusetts)
https://buildingscience.com/sites/default/files/migrate/pdf/GM_DER_Guide_2013-01-18.pdf
"In zone 5 IRC code min for basement walls is now R15 continuous insulation, so a mere 3" on the interior isn't going to cut it."
Thanks for pointing that out. I believe we're still under 2009 IRC, which requires just R10 continuous, but I will double-check. Or just add more insulation, which is never a bad thing.
@Martin Holladay - you've given me so much helpful information already. I think the only thing I'm still not quite sure on is the roof assembly.
I'll certainly bump up thickness of the exterior polyiso to meet the 41% requirement.
I was thinking of an interior vapor retarder in the attic as being necessary to prevent moist indoor air from moving through the insulation to the roof deck. But if I understand you correctly, you're saying that I don't need an interior vapor retarder? So, just to clarify, will I be fine with installing unfaced fiberglass batts directly beneath the roof deck? This will be in addition to ZIP roof sheathing and enough exterior polyiso insulation to meet the 41% requirement.
All interior rooms will be drywalled, but there will be a conditioned "crawl space" behind the attic kneewalls. I really don't want to get into the headache of trying to drywall every nook and cranny of that conditioned attic space.
One more question: does it matter if my exterior polyiso insulation is foil-faced or not? I'm planning to use recycled panels due to cost.
Foeller,
I'm going to end up repeating myself, but I'll say it again: When you have an adequately thick layer of exterior rigid foam as part of your roof assembly, (a) your roof sheathing will stay warm all winter, and (b) you won't have moisture problems (because condensation only occurs on cold surfaces), and (c) neither your building official nor building scientists will require or recommend the use of an interior vapor barrier.
你不会被要求背后的表面your kneewall with drywall.
Can you find a dense pack cellulose outfit to insulate your walls rather than use fiberglass?